
Development of apparatus for Single-sided Wet Etching and its applications in Corrugated Membrane Fabrication
This is an Open Access article distributed under the terms of the Creative Commons Attribution Non-Commercial License(https://creativecommons.org/licenses/by-nc/3.0/) which permits unrestricted non-commercial use, distribution, and reproduction in any medium, provided the original work is properly cited.
Abstract
Wet etching is more economical than dry etching and provides a uniform etching depth regardless of wafer sizes. Typically, potassium hydroxide (KOH) and tetra-methyl-ammonium hydroxide (TMAH) solutions are widely used for the wet etching of silicon. However, there is a limit to the wet etching process when a material deposited on an unetched surface reacts with an etching solution. To solve this problem, in this study, an apparatus was designed and manufactured to physically block the inflow of etchants on the surface using a rubber O-ring. The proposed apparatus includes a heater and a temperature controller to maintain a constant temperature during etching, and the hydrostatic pressure of the etchant is considered for the thin film structure. A corrugation membrane with a diameter of 800 μm, thickness of 600 nm, and corrugation depth of 3 μm with two corrugations was successfully fabricated using the prepared device.
Keywords:
Single-sided wet etching, KOH wet etching, Corrugated membrane1. INTRODUCTION
The development of silicon wafer-based micromachining processes has made it possible to develop devices with various mechanical structures as well as semiconductor processes, which has led to the commercialization of micro-electro-mechanical system (MEMS) devices. MEMS sensors can react sensitively to small physical quantities owing to their small micron-sized structures. Thus, they are used in various fields, including acoustic and vibration transducers and sensors that detect various chemical substances [1-3]. For a simple cantilever structure [4], a thin membrane structure with a thickness of less than 1 μm [5], and a structure such as a comb-drive [6], etc. are mainly used, and a more sophisticated fabrication process to improve the performance of transducers is required.
Etching can be of two types: wet and dry etching. In dry etching, because reactive gases and ions are used, the process is performed in a vacuum environment. Reactive-ion etching (RIE) is a type of dry etching. As dry etching is generally anisotropic, it is widely used in fabrication processes involving microstructures with high aspect ratios, such as semiconductors and MEMS transducers [7]. However, precision equipment is required, and the process is expensive. Furthermore, when performing a deep etch, the uniformity within the wafer is relatively poor [8]. This is a problem with processes involving a thin membrane structure. To form a thin membrane over the entire wafer, the patterns in the center must be over-etched because of the nonuniform etch rate; thus, there is a high possibility that the membrane can be destroyed or damaged.
Wet etching is generally isotropic, and a chemical reaction occurs between a wafer and an etchant. For anisotropic wet etching, etching is performed using the difference in etch rate according to the lattice direction. The etching of silicon is performed using KOH and TMAH. As wet etching can be carried out with a simple preparation and the etching rate is relatively fast, it is preferred and widely used in etching deeper than 10 μm, e.g., creating a cantilever structure or a thin membrane structure [8].
The practical drawback of wet etching is that the entire wafer is immersed in a solution to carry out the process; thus, it may be damaged if the unetched side is not coated with a passivation layer. For instance, if there is a MOSFET that has a CMOS on the front side (or a metal such as aluminum that easily reacts with KOH), wet etching is impossible [9,10]. As it is not possible to create a protective film using a photoresist when performing KOH wet etching, a protective film using poly-methyl-methacrylate (PMMA) has been suggested, but it has been reported that the adhesion between PMMA and the silicon wafer becomes a problem when etching is performed at a high temperature for a long time [11].
To overcome this problem, a method of physically blocking the etchant and the substrate using a mechanical structure and an O-ring has been proposed (instead of chemically covering the protective film) [12-15]. However, in the case of the reported device, the temperature is not controlled by itself; instead, the entire device is immersed in a KOH bath maintained at a constant temperature, or an additional device, such as an auto-leveling system to maintain a constant etchant level is required. In addition, in this method, as the wafer and etchant are in contact at only one side (to form a structure, such as a very thin film of 1 μm or less), it is important to balance the pressure (considering the hydrostatic pressure). In the previous study, this aspect was not considered, and a detailed description of the method for adjusting the pressure was not presented.
Therefore, in this study, an apparatus to compensate for the aforementioned disadvantages was designed and fabricated. Using this device, a corrugated membrane was fabricated. The corrugated thin film structure, as shown in Fig. 1, reduces the mechanical stiffness of the membrane (as the corrugation structure is placed on the boundary edge of the thin film) and is widely used in MEMS microphones that require a very high mechanical compliance [16]. The designed and fabricated (square-shaped, corrugated) membrane is composed of silicon-oxide and silicon-nitride multi-layers and has a side length of 800 μm, thickness of 0.6 μm, and corrugation depth of 3 μm with two corrugations.
2. APPARATUS DESIGN FOR SINGLE-SIDED WET ETCHING
2.1 Structure of Apparatus and Basic Working Principle
Fig. 2 shows the structure of the device for single-sided wet etching. The overall structure was designed using polytetrafluoroethylene (PTFE or Teflon), a material that is chemically resistant to KOH, and O-rings were used to seal the front and back sides of the wafer (to prevent the etchant from penetrating the back side). Sufficient pressure is applied to the O-rings using screws and threads (on the structures of the device) to ensure appropriate sealing.
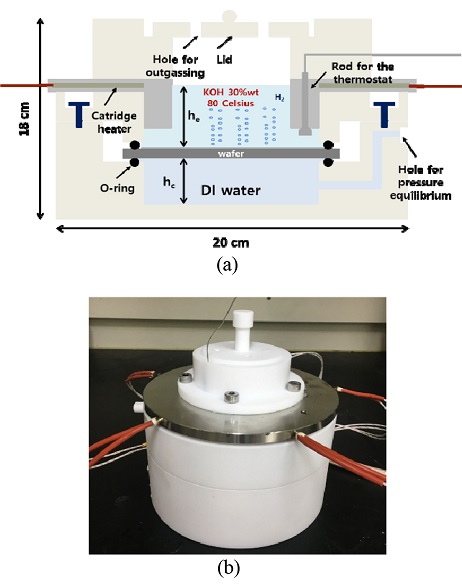
(a) Schematic figure of apparatus for single-sided wet etching, (b) Photo of the fabricated apparatus.
In wet etching (using KOH), the etch rate depends on the concentration and temperature of KOH. Mainly, a concentration of 20 to 30 wt% and a temperature of 80 to 90 °C are required, and the same conditions were used in this study [8]. A rod-shaped cartridge heater and a thermostat were used to heat the solution during etching and maintain a constant temperature. The cartridge heater does not directly come into contact with the KOH solution; it is inserted into a structure made of stainless steel to transmit heat. At the top, a structure with a lid was used. The lid has a hole and is designed to allow hydrogen gas generated during etching to escape. It also enables in-situ monitoring and prevents KOH from popping out; thus, the level of solution is maintained even after the long etching time.
A cavity is formed in the lower part of the apparatus and filled with deionized (DI) water during etching. Thus, the opposite side of the wafer on which the etching is performed can come into contact with water. The water in the closed cavity acts like a spring after reaching quasi-static equilibrium. This spring automatically balances the pressure, including hydrostatic pressure, on the micro-structure created on the wafer. The pressure balance will be discussed in the next section in detail. A vent hole connected to the cavity is located at a position higher than the wafer surface; thus, the increased volume of water during heating is allowed to escape.
2.2 Wet etching considering the hydrostatic pressure of the etchant
First, the cavity was filled with sufficient DI water; thus, the non-etched surface of the substrate came in contact with the water. Next, the bolt was tightened and the O-ring was used for sealing. After installing the stainless-steel structure, including the cartridge heater and temperature sensor, and finally, the Teflon cover structure, KOH was poured onto the surface.
If the wafer is installed in the device, the cartridge heater is turned on to keep the KOH solution within the desired temperature. If 500 μm silicon is etched using 30 wt% KOH solution at 80 to 90 °C, the process takes approximately 5 h to complete. Thus, all parts of the device (including DI water) are in thermal equilibrium before the thin film is formed. When thermal equilibrium is reached, the volume of the DI water trapped in the cavity increases by thermal expansion and is discharged from the hole.
The unetched wafer has a high mechanical stiffness so that the hydrostatic pressure KOH need not be considered at the beginning of etching. When the device and substrate reach thermal equilibrium and after all the increased volume of trapped DI water is discharged, the vent hole (for controlling the pressure of DI water) is closed. If the DI water is assumed to be completely incompressible, the trapped DI water always exerts the same repulsive force on the force applied from the substrate. That is, regardless of the height, concentration, and temperature of KOH, the pressure is always balanced. Therefore, the process can be safely carried out even if a highly elastic structure (such as a corrugated thin film with a thickness of less than 1 μm) is created.
It is necessary to check whether the DI water at 80 °C has sufficient incompressible properties. Water can be approximated as an incompressible fluid in many cases; however, in the fabrication of a thin film, owing to its small size, a large deformation of the thin film may occur even with a small change in volume. As the change in volume of water due to the thin film is very small compared to the total volume of water, the process could be considered isothermal. The definition of isothermal compressibility (κT) and its value can be expressed as [17]
(1) |
If the volume of the cavity is VC, the volume changed by the hydrostatic pressure of KOH is as follows:
(2) |
where ρKOH represents the density of KOH, g is the acceleration due to gravity, and he is the height of KOH. As pressure is transmitted only through the thin film structure, the displacement of the thin film can be obtained by dividing the volume increment by the entire area of the thin film. That is, when the mechanical stiffness of the thin film is ignored, the distance of the thin film moved by the KOH solution is as follows.
(3) |
Where ds is the displacement of the membrane, Ad is the total membrane area in the wafer, hc is the height of the cavity, and m is the ratio of the membrane area over the entire wafer. Using Eq. (3) and assuming that the KOH solution and the cavity height are 5 cm and the thin film occupies 40% of the total wafer area, the displacement of each membrane is approximately 40 nm. As the membrane thickness is much thicker than the displacement, the displacement can be considered sufficiently small such that there is no damage to the membrane.
3. FABRICATION PROCESS
A six-inch, total thickness of 500 μm, <100> crystal orientation, and a P-type double-sided polished (DSP) silicon wafer was used. First, 100 nm of a silicon oxide film was formed by thermal oxidation, [Step (a)] and 100 nm of SiO2 and 3 μm of Si were dry-etched to create a corrugation part. Dry etching resulted in a rectangular corrugation pattern. [Step (b)] Next, 500 nm of low-stress silicon nitride was deposited using low-pressure chemical vapor deposition (LPCVD). [Step (c)] For use as a thin membrane of an MEMS microphone, 150 nm of Ni and Au metal film was deposited with a sputter and an E-beam evaporator, respectively, and patterning was carried out through a lift-off process. [Step (d)] Next, for the KOH wet etching, a silicon oxide/nitride film was etched on the back side of the wafer through dry etching (using PR patterning). [Step (e)] Finally, using the apparatus presented in this study, KOH wet etching was performed without damaging the front side of the wafer. The KOH concentration was 25-30 wt%, and the fabrication of the membrane was completed after approximately 5 h at 80 °C to 90 °C.
4. RESULTS AND DISCUSSIONS
Fig. 4 shows the fabricated corrugated membrane. Based on the optical microscopy image, the corrugation membrane was successfully fabricated. In addition, there was no destroyed membrane on the entire wafer, and most of the membrane was manufactured as designed.
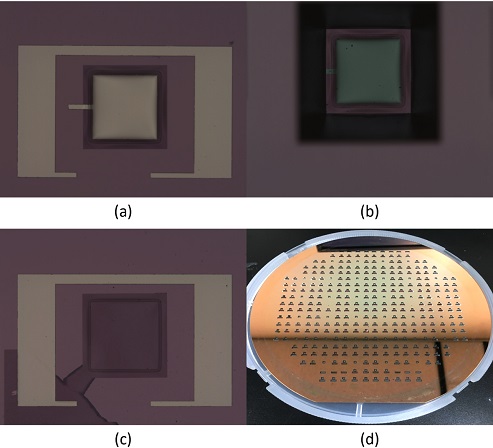
Fabricated Corrugated Membrane; (a) Optical microscopy image of the front and (b) backside of the corrugated membrane (c) Failed pattern, (d) Entire wafer picture.
In wet etching, a protective film using positive photoresist (PR) AZ GXR-601 (46cp) was formed on the entire front surface to check whether the KOH solution penetrated the front surface (side to be protected) of the substrate. In the case of positive PR, as it is highly reactive to the KOH solution, PR is removed from the substrate when it comes into contact with KOH. However, when using the proposed apparatus, the PR of the front side is completely maintained even after the etching is completed, which proves that the KOH solution does not penetrate.
As a mask material for KOH wet etching, 500 nm of a silicon nitride film (deposited using LPCVD) was used, which was well maintained during etching. However, after a long wet-etching process, a difference in color (between the part being in direct contact with KOH and the part that was not) was confirmed visually, and it is expected that a fine degree of etching was performed. In addition, as shown in Fig. 4(c), one membrane was not destroyed after wet etching; however, it was produced in an undesirable shape. This is because the width of the silicon nitride layer between adjacent patterns is designed to be approximately 100 μm, and when wet etching is performed for a long time, the silicon nitride layer between the patterns cannot withstand and collapse. Thus, it can be assumed that maintaining a distance of more than 200 μm between the patterns will produce a stable result.
As in-situ monitoring is possible during etching, one can determine the end point. In particular, when using KOH, hydrogen gas is generated. Therefore, when etching is being actively performed, many bubbles are formed, and the solution appears cloudy. When etching is completed, the solution becomes transparent, as hydrogen gas is not generated. This signals the end of the process.
5. CONCLUSIONS
In this study, an apparatus for wet etching of a silicon wafer was designed and fabricated. The proposed apparatus design is composed of a PTFE-based (Teflon-based) device with an O-ring for sealing, and a temperature maintenance metal structure (including a thermostat and cartridge heater). It also includes a lid structure for in-situ monitoring and a pressure vent hole (considering the changes in volume and temperature). Unlike existing devices, the temperature can be adjusted. In addition, it is designed such that the delicate MEMS structure in the wafer is not affected by the hydrostatic pressure of the etchant. A KOH solution of 30 wt%, 85° Celsius was used for silicon etching, and the etching rate was measured to be 2.1 μm/min. Using the proposed apparatus, a circular corrugation diaphragm with a diameter of 800 μm, a thickness of 600 nm, and a corrugation depth of 3 μm with two corrugations was successfully fabricated on a six-inch silicon wafer.
Acknowledgments
This work was supported by the Technology Innovation Program (20004285) funded by the Ministry of Trade, Industry & Energy (MOTIE, Korea)
REFERENCES
-
D. T. Martin, J. Liu, K. Kadirvel, R. M. Fox, M. Sheplak, and T. Nishida, “A micromachined dual-backplate capacitive microphone for aeroacoustic measurements”, J Microelectromech. Syst., Vol. 16, No. 6, pp. 1289-1302, 2007.
[https://doi.org/10.1109/JMEMS.2007.909234]
-
A. Ravi Sankar and S. Das, “A very-low cross-axis sensitivity piezoresistive accelerometer with an electroplated gold layer atop a thickness reduced proof mass”, Sens. Actuators A, Vol. 189, pp. 125-133, 2013.
[https://doi.org/10.1016/j.sna.2012.09.025]
-
H. Nazemi, A. Joseph, J. Park, and A. Emadi, “Advanced Micro- and Nano-Gas Sensor Technology: A Review”, Sensors, Vol. 19, No. 6, pp. 1285(1)-1285(23), 2019.
[https://doi.org/10.3390/s19061285]
-
S. Saadon and O. Sidek, “A review of vibration-based MEMS piezoelectric energy harvesters”, Energy Convers. Manag., Vol. 52, No. 1, pp. 500-504, 2011.
[https://doi.org/10.1016/j.enconman.2010.07.024]
-
M. Pedersen, W. Olthuis, and P. Bergveld, “A silicon condenser microphone with polyimide diaphragm and backplate”, Sens. Actuators A, Vol. 63, No. 2, pp. 97-104, 1997.
[https://doi.org/10.1016/S0924-4247(97)01532-X]
-
K. Oda, H. Takao, K. Terao, T. Suzuki, F. Shimokawa, I. Ishimaru, and F. Oohira, “Vertical comb-drive MEMS mirror with sensing function for phase-shift device”, Sens. Actuators A, Vol. 181, pp. 61-69, 2012.
[https://doi.org/10.1016/j.sna.2012.04.007]
- S. D. Senturia, Microsystem design, Kluwer Academic Publishers, New York, Boston, Dordrecht, London, Moscow, pp. 67-71, 2002.
- Y. B. Gianchandani, O. Tabata, and H. P. Zappe, Comprehensive microsystems, Elsevier B.V., Amsterdam, pp. 183-216, 2008.
- J. Laconte, D. Flandre, and J.-P. Raskin, Micromachined thin-film sensors for SOI-CMOS co-integration, Springer Science & Business Media, Dordrecht, pp. 17-45, 2006.
-
K. R. Williams, K. Gupta, and M. Wasilik, “Etch rates for micromachining processing-part II”, J Microelectromech. Syst., Vol. 12, No. 6, pp. 761-778, 2003.
[https://doi.org/10.1109/JMEMS.2003.820936]
- D. Bodas, S. J. Patil, V. Krishnamurthy, and S. J. J. o. t. I. I. o. S. Gangal, “PMMA as an etch mask for silicon micromachining a feasibility study”, J Indian Inst. Sci., Vol. 81, No. 6, pp. 645-651, 2013.
-
J. T. Kung, A. N. Karanicolas, and H.-S. Lee, “A compact, inexpensive apparatus for one-sided etching in KOH and HF”, Sens. Actuators A, Vol. 29, No. 3, pp. 209-215, 1991.
[https://doi.org/10.1016/0924-4247(91)80017-J]
- J. Brugger, G. Beljakovic, M. Despont, H. Biebuyck, N. F. de Rooij, and P. Vettiger, “High-yield wafer chuck for single-sided wet etching of MEMS structures”, Proc. Int. Solid State Sens. Actuators Conf. (Transducers '97), pp. 711-713, Chicago, USA, 1997.
- N. Kummer, J. Marek, M. Willmann, and G. Findler, “Device for one-sided etching of a semiconductor wafer", U.S. Patent No. 5,324,410. 28 Jun. 1994.
- K. Sooriakumar, S. A. Switzer, K. E. Stegall, T. J. Dunlap, and C. M. Albrecht, “Substrate holder and method of use”, U.S. Patent No. 5,578,167. 26 Nov. 1996.
-
A. Dehé, M. Wurzer, M. Füldner, and U. Krumbein, “A4. 3-The infineon silicon MEMS microphone”, Proc. Sens. 2013, pp. 95-99, Germany, 2013.
[https://doi.org/10.5162/sensor2013/A4.3]
-
G. S. J. J. o. C. Kell and E. Data, “Density, thermal expansivity, and compressibility of liquid water from 0. deg. to 150. Deg: Correlations and tables for atmospheric pressure and saturation reviewed and expressed on 1968 temperature scale”, J. Chem. Eng. Data, Vol. 20, No. 1, pp. 97-105, 1975.
[https://doi.org/10.1021/je60064a005]