
Piezoelectric Ultrasound MEMS Transducers for Fingerprint Recognition
This is an Open Access article distributed under the terms of the Creative Commons Attribution Non-Commercial License(https://creativecommons.org/licenses/by-nc/3.0/) which permits unrestricted non-commercial use, distribution, and reproduction in any medium, provided the original work is properly cited.
Abstract
As mobile electronics become smarter, higher-level security systems are necessary to protect private information and property from hackers. For this, biometric authentication systems have been widely studied, where the recognition of unique biological traits of an individual, such as the face, iris, fingerprint, and voice, is required to operate the device. Among them, ultrasound fingerprint imaging technology using piezoelectric materials is one of the most promising approaches adopted by Samsung Galaxy smartphones. In this review, we summarize the recent progress on piezoelectric ultrasound micro-electro-mechanical systems (MEMS) transducers with various piezoelectric materials and provide insights to achieve the highest-level biometric authentication system for mobile electronics.
Keywords:
Piezoelectric, MEMS, Ultrasound transducer, Fingerprint, Security1. INTRODUCTION
Security issues are becoming more critical with the increasing use of mobile electronics such as smartphones, which not only create, transmit, and store an individual’s private information but also enable personal financial management. In this regard, biometrics-based authentication technologies have attracted significant attention as promising candidates for high-level security systems in mobile electronics. For mobile applications, several requirements must be met, such as low power consumption, small size, low cost, forgery difficulty, and convenience. Among the many biometrics, fingerprint recognition technology has emerged as an attractive security system that readily meets these requirements. However, the common detection methods of fingerprints, whether capacitive or optical, are vulnerable to hacking by fingerprint copying phantoms and do not function well in dirty and/or moist environments. To overcome these limitations, an ultrasound fingerprint recognition method was proposed, which can take advantage of the delicate 3D structural variations of the ridges and valleys in one’s fingerprints. Moreover, they are more reliable in dirty and moist environments.
The principle of fingerprint recognition using ultrasound is the same as that of biomedical ultrasound imaging. Ultrasound transducers are key devices that can generate continuous or pulsed ultrasound waves and simultaneously sense incoming ultrasound signals. By detecting the time delays of ultrasounds reflected from the ridges and valleys, they can reconstruct the 3D structure of fingerprints. To obtain 3D structural information on fingerprints, a beam-forming technique is necessary where the ultrasound beam can be focused and steered along the x-and y-directions. As this is possible because of the interference phenomenon of ultrasound, multiple sources of ultrasound, that is, a 2D array of ultrasound cells, are needed. Each cell should be independently driven by controlled electric signals to steer and focus on a collective ultrasound beam.
A micromachined ultrasound transducer (MUT) is an ideal platform for fabricating a two-dimensional (2D) array of ultrasound cells in a small device using the MEMS process. There are two different types of MUTs: piezoelectric MUT (pMUT) and capacitive MUT (cMUT), as shown in Fig. 1(a) and (b), respectively. For a pMUT, a piezoelectric material layer is the essential element that converts electric fields into mechanical vibrations (actuating) and vice versa (sensing). For the cMUT, the electrostatic force and capacitance change between two electrodes separated by a vacuum gap are used for actuating and sensing, respectively. From the perspective of mobile applications, pMUT is preferred over cMUT as cMUT is weak to mechanical impact and should be operated under several tens of DC bias voltage. In this review, we summarize the recent progress in pMUT devices for fingerprint recognition systems and discuss the potential applications of pMUT beyond fingerprint recognition.
2. PIEZOELECTRIC MATERIALS FOR pMUT
While various piezoelectric materials have been studied for pMUT application, we introduce some representative candidates considering the figure of merit (FOM) of pMUT. pMUT generates ultrasound by the vibration followed by vertical deflection of piezoelectric membrane when driving voltage is applied. The transverse piezoelectric constant of thin film, e31,f, indicates the ratio between deflected strain and applied voltage, indicating the relation between output sound pressure and input voltage. pMUT sensing is done by the vibration of piezoelectric membrane as acoustic wave is received. This mode is determined by the constants in form of e31,f / εr33ε0, while εr33 and ε0 are relative dielectric constant and dielectric constant of vacuum. Combining key factors of transmitting and sensing operations, the FOM of pMUT is (e31,f)2 / εr33ε0 [2].
2.1 PZT
Pb(Zr,Ti)O3 (PZT) is a piezoelectric perovskite oxide that is a solid solution of PbZrO3 and PbTiO3. The Zr/Ti ratio at the B-site determines the crystal structure and material properties. A large piezoelectric property emerges around Zr:Ti = 52:48, known as the morphotropic phase boundary (MPB), which is an almost vertical line in the temperature versus composition phase diagram, where a transition occurs between the tetragonal and rhombohedral ferroelectric phases. The piezoelectric property of PZT can further be tuned by impurity doping to make it “hard” or “soft,” which denotes the feasibility of the dipole movement. Because PZT is a ferroelectric material with switchable polarization by an external electric field, a poling process allows the use of polycrystalline PZT materials with high piezoelectric properties. PZT has a piezoelectric constant nearly an order of magnitude higher than that of AlN [3]. Because of the high piezoelectric properties of PZT, an exemption has been applied to PZT from the RoHS Restriction of Hazardous Substances since 2003.
2.2 AlN
AlN is a III-V compound with a wultzite structure which shows two polarities since the basal plane is determined between alternating layers of Al- and N-. Thus AlN thin film in polycrystalline form may have no piezoelectricity when two polarities are equally distributed [4, 5]. AlN is known for its piezoelectric tolerance to high temperature (> 1000 °C), and can be applied in harsh environments that require robust thermal stability [6]. AlN has a relatively low piezoelectric constant (e31,f) compared with PZT, which leads to a lower output pressure of ultrasound from AlN-based pMUT. However, because AlN has a lower dielectric constant ε33 than PZT, the sensitivity of AlN-based pMUT is high [3]. As has been reported recently, doping can significantly modify the properties of AlN. Wang et al [7]. reported an Sc: AlN-based pMUT that showed a 20 % increase in the electromechanical coupling coefficient (kt2) and a triple increase in the output pressure with respect to the value of an AlN-based pMUT with the same geometry and fill factor under the same measurement conditions. Moreover, Fichtner et al. reported that AlN also exhibits ferroelectric behavior upon Sc doping [8].
2.3 PVDF
Polyvinylidene fluoride (PVDF), a semi-crystalline polymer polymerized with H2C=CF2 monomers, is well known for its higher piezoelectric coefficient than that of other piezoelectric polymers. The piezoelectric performance is enhanced by defects generated during the connection between two CF2 groups or CH2 groups. Defects induce an increase in polarization, which leads to an improvement in the piezoelectric response. The β-phase has the best piezoelectric performance of the five known phases of PVDF (α, β, γ, δ, and ε) because all dipole moments are aligned. Studies have been conducted where further control of the crystal orientation of PVDF was achieved by adding trifluoroethylene (TrFE) [9]. Qualcomm fabricated fingerprint sensors that successfully conducted under-display ultrasonic detection using PVDF-TrFE [10-12]. Even though the material shows a relatively poorer piezoelectric response than PZT, it has a dielectric constant similar to that of AlN [13]. Thus, with the help of a charge amplifier, the PVDF-based pMUT could be implemented in commercial devices [10-12].
3. pMUT DEVICES
3.1 MEMS Fabrication Process
To fabricate a pMUT, piezoelectric membranes must have sufficient empty space for vibration. Unlike cMUT, empty spaces in pMUT do not have to be between the device layers. Thus, after fabricating piezoelectric films through methods like sputtering [7, 18, 19], sol-gel [20] and spin coating [21], void fabrication can be performed at the final stage using a deep reactive ion etching (DRIE) method, as shown in Fig. 3. The piezoelectric thin film with top and bottom electrodes must be integrated onto a passive layer, mostly Si, to convert the lateral motion (31 mode) of the piezoelectric layer into vertical bending motion. Because the thickness of the Si passive layer must be precisely controlled, silicon on insulator (SOI) wafers are usually used, where the buried oxide layer works as an etch-stop layer during DRIE of the backside handling Si.
3.2 Array Structure of Ultrasound Cells
Deposited films are patterned according to array structures such as 1D, 2D row-column, and 2D accommodated with application-specific integrated circuits (ASIC). The 1D array structure cannot operate the imaging process in a direction parallel to the array because membrane cells in the same array are controlled simultaneously through a single top electrode pad. Thus, the 1D array requires the mechanical movement of the device along the direction of the arrays during scanning. 2-D arrays not only reduce the extra time required for moving the transducer but also allow more options for scanning with beam steering and focusing on 2-dimensional control. However, 2-D arrays pose problems in complex imaging, scanning, and system organization caused by numerous interconnections between each cell and electrode. Row-column addressing can solve this problem by reducing the interconnections without decreasing the number of cell elements [23]. For example, for N×N arrays, the number of wires can be lowered to 2N. To achieve ultrasound imaging with better control of each cell element, ASIC can be organized to have pMUT and complementary metal-oxide semiconductor (CMOS) integration by having a one-on-one connection between each cell and the CMOS transistor, as shown in Fig. 4(c). Because CMOS is vulnerable to high temperatures of approximately 525 °C [24], CMOS and piezoelectric diaphram MEMS are fabricated separately and bonded to form interconnections through flip chip bonding, which provides a large number of shorter electric contacts compared with wire bonding. In flip chip bonding, thermocompression is used depending on the eutectic temperature of the bonding material, and the thermosonic method is used when the system requires a much lower temperature and pressure [25].
3.3 Geometry of Ultrasound Cells
For fingerprint sensors, the standard resolution is 500 DPI, the same as that required by FBI-compliant systems [27]. To enhance the lateral resolution of the fingerprint sensor, the cell size and pitch length should be diminished. This interferes with the acoustic output and fill factor for the CMOS-combined pMUT because the area for interconnection remains the same whereas the active area decreases. Jiang et al [28]. reported an increase in the fill factor and output pressure of an ultrasonic fingerprint sensor using a rectangular cell design. Figs. 5(c) and (d) show the output pressure of the rectangular and circular pMUT at each resonance frequency for a hydrophone distance of 220 μm and 400 μm. The measured acoustic surface pressures for each pMUT are 70.8 and 41.9 kPa, which are caused by the three times higher fill factor.
Tanaka. et al [29]. adopted a hexagonal array to upgrade the imaging system and simplify the imaging operation. The hexagonal arrangement allows the densification of operating elements with a relatively smaller pitch and larger cell size, which contributes to the enhancement of the imaging resolution and sound pressure. Moreover, only two types of distance information are required to perform beamforming, whereas for the orthogonal arrangement, this number is three. A time delay should exist for each input signal of the orthogonal array, which is difficult to achieve for such an arrangement because the elements have a common electrode in either the row or column direction.
3.4 Fingerprint Imaging by pMUT
Tang et al [26]. reported an ultrasonic fingerprint sensor on a chip containing pMUT combined with CMOS ASIC through eutectic bonding. This AlN pMUT provided a 591 × 438 DPI resolution, comprising 110 × 56 rectangular cells with a pitch of 43 μm. A polydimethylsiloxane (PDMS) coupling layer was placed on an ultrasonic sensor for acoustic impedance matching. The surface and inner tissue of the fingerprint, known as the epidermis and dermis, respectively, were scanned to provide images, as shown in Fig. 6(a). Ultrasonic waves exhibit a 100 % reflection caused by the air-filled valley part of the fingerprint, resulting in a dark pattern in the image. Ultrasound penetrates the ridge and is reflected near the dermis by an impedance mismatch. Analyzing the received echoes with a time delay separates the epidermal and dermal images in a single operation.
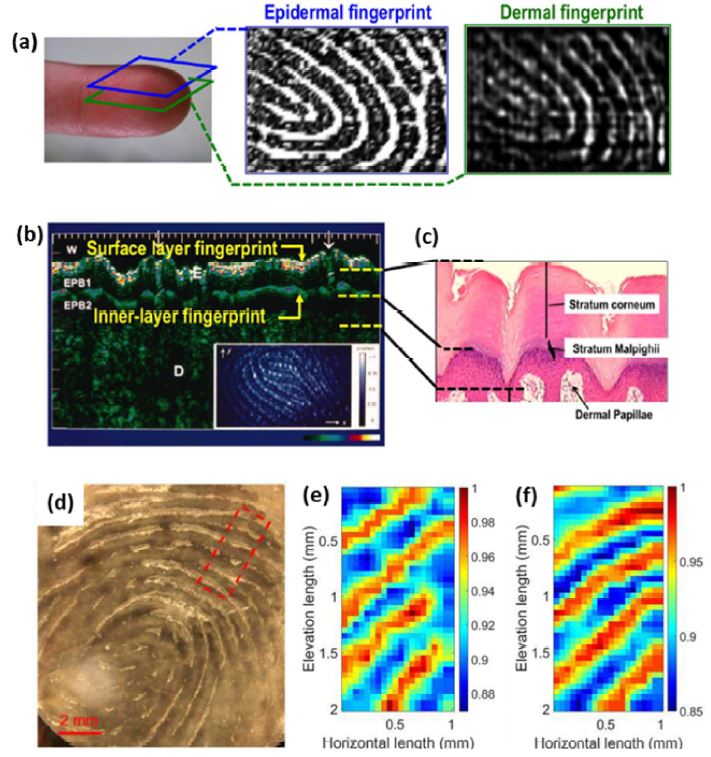
(a) Dermal and (b) epidermal images acquired using pMUT. (b) High-resolution ultrasound sonograph of a human fingertip. (c) Anatomy cross-section of human fingertip. (a-c) Reproduced with permission from Ref. [26]. (d) PMDS fingerprint phantom and its image, acquired under (e) glass layer and (f) OLED display. (d-f) Reproduced with permission from Ref. [17].
To use fingerprints for biometric authentication in smartphones, Peng et al [17]. reported a piezoelectric polymer-based pMUT for under-display fingerprint sensing. 10 μm thick and 1 × 1 mm2 P(VDF-TrFE) was set as a single element with E-solder as the backing layer and electrode. The PDMS fingerprint phantom was scanned by the mechanical movement of the transducer. Images with a resolution of 500 × 500 DPI resolution and 70.7 μm lateral resolution were acquired with a glass layer placed between the pMUT and phantom. The lateral resolution of the acquired image through the OLED touch screen was 68.9 μm, providing a similar quality of image regardless of whether the phantom was under the glass or display screen, as shown in Figs. 6(e) and 6(f). pMUT-based fingerprint-imaging technologies are listed in Table 2.
4. CONCLUSIONS
We reviewed the recent progress in fingerprint imaging technology using ultrasound MEMS transducers for mobile security systems. Piezoelectric micromachined ultrasound transducers are promising candidates because they have a simple structure and require low driving power compared with capacitive micromachined ultrasound transducers. The performance of pMUT is largely dependent on the piezoelectric properties of piezoelectric thin films. Among the many piezoelectric materials, PZT (oxide), AlN (nitride), and PVDF (polymer) have been explored to realize pMUT-based fingerprint-recognition systems.
In general, PZT exhibits the best piezoelectric properties. However, the existence of Pb is a disadvantage because of ever-increasing global environmental protection policies. AlN exhibits excellent sensitivity owing to its low dielectric constant. However, the power required to generate ultrasound is low owing to the low piezoelectric coefficient. PVDF has moderate piezoelectric properties and is currently used in commercial devices. Moreover, the performance of the pMUT is determined by the geometry of each vibrating cell, and the lateral size and thickness of the cell as well as the mechanical properties of the passive layer, affect the resonance frequency and displacement. To build a fingerprint recognition system, pMUT devices should be integrated with an ASIC. Each piezoelectric vibrating cell can be directly connected to a switching transistor by using flip-chip bonding techniques.
Further improvement of the pMUT’s performance will broaden its applications beyond fingerprint recognition systems. To realize hyperactive ultrasound transducers, it is necessary to develop large piezoelectric materials that can surpass the piezoelectric properties of PZT, AlN, and PDVF. Relaxor-ferroelectric single crystals are known to exhibit superior piezoelectric properties compared to conventional PZTs. Recently, by doping the A-site with rare-earth elements into PMN-PT, a representative relaxor-ferroelectric, a longitudinal piezoelectric coefficient (d33) of 3400–4000 pC/N was reported30, the largest value so far. If these materials can be integrated into Si, the pMUT performance will be significantly enhanced to achieve much higher levels of security; for example, the 3D structure of fingerveins and blood flows can be precisely detected, which are very difficult to forge.
Developing high-performance lead-free piezoelectric thin films is also necessary. Significant progress has been made in achieving lead-free piezoelectric bulk materials. However, progress in the development of lead-free piezoelectric thin films has been slow. To overcome this environmental issue, it is critical to develop a thin-film growth technique for high-performance lead-free piezoelectric materials on the wafer scale.
Acknowledgments
The authors gratefully acknowledge financial support from the Samsung Research Funding & Incubation Center for Future Technology (SRFC-MA1702-03) and National Research Foundation of Korea (NRF) grant funded by the Ministry of Science and ICT (NRF-2020M3D1A2101933).
References
-
Y. Qiu, J. V. Gigliotti, M Wallace, F. Griggio, C. E. M. Demore, S. Cochran, and S. Trolier-McKinstry, “Piezoelectric Micromachined Ultrasound Transducer (PMUT) Arrays for Integrated Sensing, Actuation and Imaging”, Sens., Vol. 15, No. 4, pp. 8020-8041, 2015.
[https://doi.org/10.3390/s150408020]
-
P. N. Thao, S. Yoshida, and S. Tanaka, “Fabrication and Characterization of PZT Fibered-Epitaxial Thin Film on Si for Piezoelectric Micromachined Ultrasound Transducer”, Micromachines, Vol. 9, No. 9, p. 455, 2018.
[https://doi.org/10.3390/mi9090455]
-
S. Trolier-McKinstry and P. Muralt, “Thin Film Piezoelectric for MEMS”, J.Electroceram., Vol. 12, No. 1, pp. 7-17, 2004.
[https://doi.org/10.1023/B:JECR.0000033998.72845.51]
-
K. Tonisch, V. Cimalla, C. Foerster, H. Romanus, O.Ambacher, and D. Dontsov, “Piezoelectric Properties of Polycrystalline AlN Thin Films for MEMS Application”, Sens. Actuators A: Phys., Vol. 132, No. 2, pp. 658-663, 2006.
[https://doi.org/10.1016/j.sna.2006.03.001]
-
R. M. R. Pinto, V. Gund, C. Calaza, K. K. Nagaraja, and K. B. Vinayakumar, “Piezoelectric Aluminum Nitride Thin-Films: A Review of Wet and Dry Etching Techniques”, Microelectron. Eng., p.111753, 2022.
[https://doi.org/10.1016/j.mee.2022.111753]
- B. R. Tittmann, D. Parks, and S. O. Zhang, “High Temperature Piezoelectrics – A Comparison”, Proc. of 13th Int. Symp. on Nondestruct. Charact. of Mater., Le Mans, France, pp. 20-24, 2013.
-
Q. Wang, Y. Lu, S. Fung, X. Jiang, S. Mishin, Y. Oshmyansky, and D.A. Horsley, “Scandim Doped Aluminum Nitride Based Piezoelectric Micromachined Ultrasound Transducers”, Proc. of Solid-State Sens., Actuators, Microsyst. Workshop, pp. 436-439, 2016.
[https://doi.org/10.31438/trf.hh2016.116]
-
S. Fichtner, N. Wolff, F. Lofink, L. Kienle, and B. Wagner, “AlScN: A III-V Semiconductor Based Ferroelectric”, J. Appl. Phys., Vol. 125, No. 11, p. 114103, 2019.
[https://doi.org/10.1063/1.5084945]
-
K. S. Ramadan, D. Sameoto, and S. Evoy, “A Review of Piezoelectric Polymers as Functional Materials for Electromechanical Transducers”, Smart Mater. Struct., Vol. 23, No. 3, p. 033001, 2014.
[https://doi.org/10.1088/0964-1726/23/3/033001]
- II. J. C. Kitchens, J. K. Schneider, and S. M. Gojevic, “Ultrasonic Receiver with Coated Piezoelectric Layer”, U.S. Patent 14/175,876, 07 Feb., 2014.
- J. C. Kitchens, J. K. Schneider, and S. M. Gojevic, “Piezoelectric Force Sensing Array”, U. S. Patent 14/071,320, 04 Nov., 2013.
- Y. Lu, H. V. Panchawagh, K. D. Djordjev, J. H. Seo, N. I. Buchan, C.-J. Tseng, and T. Kao, “Ultrasonic Fingerprint Sensor with Flexible Substrate”, U.S. Patent 11/126,814, 29 Jul., 2019.
- Y. Jiang, S. Shiono, H. Hamada, T. Fujita, K. Higuchi, and K. Maenaka, “Low-Frequency Energy Harvesting Using a Laminated PVDF Cantilever with a Magnetic Mass”, Power MEMS, 2010, p. 375375, 2010.
- https://en.wikipedia.org/wiki/Lead_zirconate_titanate, (retrieved on Aug. 29, 2022).
- https://en.wikipedia.org/wiki/Aluminium_nitride, (retrieved on Aug. 29, 2022).
-
T. Wu, H. Jin, S. Dong, W. Xuan, H. Xu, L. Lu, Z. Fang, S. Huang, X. Tao, L. Shi, S. Liu, and J. Luo, “A Flexible Film Bulk Acoustic Resonator Based on β-Phase Polyvinylidene Fluoride Polymer”, Sensors, Vol. 20, No. 5, p. 1346, 2020.
[https://doi.org/10.3390/s20051346]
-
C. Peng, M. Chen, H. Wang, J. Shen, and X. Jiang, “P(VDF-TrFE) Thin-Film-Based Transducer for Under-Display Ultrasonic Fingerprint Sensing Applications”, IEEE Sensors J., Vol. 20, No. 19, pp. 11221-11228, 2020.
[https://doi.org/10.1109/JSEN.2020.2997375]
-
Y. Lu and D. A. Horsley, “Modeling, Fabrication, and Characterization of Piezoelectric Micromachined Ultrasonic Transducer Arrays Based on Cavity SOI Wafers”, J. Microelectromechanical Syst, Vol. 24, No. 4, pp. 1142-1149, 2015.
[https://doi.org/10.1109/JMEMS.2014.2387154]
-
E. Shin, H. G. Yeo, A. Yeon, C. Jin, W. Park, S.-C. Lee, and H. Choi, “Development of a High-Density Piezoelectric Micromachined Ultrasonic Transducer Array Based on Patterned Aluminum Nitride Thin Film”, Micromachines, Vol. 11, No. 6, p. 623, 2020.
[https://doi.org/10.3390/mi11060623]
-
Y.-Q. Chen, Y.-X. Li, Y. Chen, Z.-Y. Ju, L.-Q. Tao, Y. Pang, Y. Yang, and T.-L. Ren, “Large-Scale and High-Density pMUT Array Based on Isolated Sol-Gel PZT Membranes for Fingerprint Imaging”, J. Electrochem. Soc., Vol. 164, No. 7, pp. B337-B381, 2017.
[https://doi.org/10.1149/2.0891707jes]
-
C. Chao, T.-Y. Lam, K.-W. Kwok, and H. L. W. Chan, “Piezoelectric Micromachined Ultrasonic Transducers Based on P(VDF-TrFE) Copolymer Thin Films”, Proc. of 15th ieee Int. Symp. Appl. Ferroelectr., NC, USA, pp. 120-123, 2006.
[https://doi.org/10.1109/ISAF.2006.4387848]
-
C. Sun, Q. Shi, M. S. Yazici, T. Kobayashi, Y. Liu, and C. Lee, “Investigation of Broadband Characteristics of Multi-Frequency Piezoelectric Micromachined Ultrasonic Transducer (MF-pMUT)”, IEEE Sens. J., Vol. 19, No. 3, pp. 860-867, 2018.
[https://doi.org/10.1109/JSEN.2018.2878785]
-
L. L. Wong, A. I. Chen, Z. Li, A. S. Logan, and J. T. Yeow, “A row-column addressed micromachined ultrasonic transducer array for surface scanning applications”, Ultrasonics, Vol. 54, No. 8, pp. 2072-2080, 2014.
[https://doi.org/10.1016/j.ultras.2014.07.002]
-
S. Sedky, A. Witvrouw, H. Bender, and K. Baert, “Experimental Determination of the Maximum Post-Process Annealing Temperature for Standard CMOS Wafers”, IEEE Trans. Electron Devices, Vol. 48, No. 2, pp. 377-385, 2001.
[https://doi.org/10.1109/16.902741]
- M. R. Lim, Z. Sauli, H. Aris, V. Retnasamy, C. Lo, K. Muniandy, N. Khan, and C. S. Foong, “The Optimization of Ultrasonic Power and Bonding Time for Thermosonic Flip Chip Bonding”, AIP Conf. Proc, Vol. 2045, No. 1, p. 020094, 2018.
-
H.-Y. Tang, Y. Lu, X. Jiang, E. J. Ng, J. M. Tsai, D. A. Horsley, and B. E. Boser, “3-D Ultrasonic Fingerprint Sensor-on-a-Chip”, IEEE J. Solid-State Circuits, Vol. 51, No. 11, pp. 2522-2533, 2016.
[https://doi.org/10.1109/JSSC.2016.2604291]
- https://www.biometrika.it/eng/wp_scfing.html, (retrieved on Aug. 23, 2022).
-
X. Jiang, Y. Lu, H.-Y. Tang, J. M. Tsai, E. J. Ng, M. J. Daneman, B. E. Boser, and D. A. Horsley, “Monolithic Ultrasound Fingerprint Sensor”, Microsyst. Nanoeng., Vol. 3, No. 1, p. 17059, 2017.
[https://doi.org/10.1038/micronano.2017.59]
-
Z. Liu, S. Yoshida, D. A. Horsley, and S. Tanaka, “Fabrication and characterization of row-column addressed pMUT array with monocrystalline PZT thin film toward creating ultrasonic imager”, Sens. Actuators A: Phys., p. 113666, 2022.
[https://doi.org/10.1016/j.sna.2022.113666]
-
L. Fei, M. J. Cabral, B. Xu, Z. Cheng, E. C. Dickey, J. M. LeBeau, J. Wang, J. Luo, S. Taylor, W. Hackenberger, L. Bellaiche, Z. Xu, L.-Q. Chen, T. R. Shrout, and S. Zhang, “Giant Piezoelectricity of Sm-doped Pb(Mg1/3Nb2/3)O3-PbTiO3 Single Crystals”, Sci., Vol. 364, No. 6437, pp. 264-268, 2019.
[https://doi.org/10.1126/science.aaw2781]
-
Y. Lu, H. Tang, S. Fung, Q. Wang, J. M. Tsai, M. Daneman, B. E. Boser, and D.A. Horsley, “Ultrasonic Fingerprint Sensor Using a Piezoelectric Micromachined Ultrasonic Transducer Array Integrated with Complementary Metal Oxide Semiconductor Electronics”, Appl. Phys. Lett., Vol. 106, No. 26, p. 263503, 2015.
[https://doi.org/10.1063/1.4922915]