
BaTiO3 압전나노입자와 폴리머로 제작된 비납계 압전복합체의 스트레쳐블 압전 센서 어레이로의 적용 연구
This is an Open Access article distributed under the terms of the Creative Commons Attribution Non-Commercial License(https://creativecommons.org/licenses/by-nc/3.0/) which permits unrestricted non-commercial use, distribution, and reproduction in any medium, provided the original work is properly cited.
Abstract
Piezoelectric energy harvesting has attracted increasing attention over the last decade as a means for generating sustainable and long-lasting energy from wasted mechanical energy. To develop self-powered wearable devices, piezoelectric materials should be flexible, stretchable, and bio-eco-friendly. This study proposed the fabrication of stretchable piezoelectric composites via dispersing perovskite-structured BaTiO3 nanoparticles inside an Ecoflex polymeric matrix. In particular, the stretchable piezoelectric sensor array was fabricated via a simple and cost-effective spin-coating process by exploiting the piezoelectric composite comprising of BaTiO3 nanoparticles, Ecoflex matrix, and stretchable Ag coated textile electrodes. The fabricated sensor generated an output voltage of ~4.3 V under repeated compressing deformations. Moreover, the piezoelectric sensor array exhibited robust mechanical stability during mechanical pushing of ~5,000 cycles. Finite element method with multiphysics COMSOL simulation program was employed to support the experimental output performance of the fabricated device. Finally, the stretchable piezoelectric sensor array can be used as a self-powered touch sensor that can effectively detect and distinguish mechanical stimuli, such as pressing by a human finger. The fabricated sensor demonstrated potential to be used in a stretchable, lead-free, and scalable piezoelectric sensor array.
Keywords:
Energy harvesting, Piezoelectric, BaTiO3, Stretchable, Sensor array1. 서 론
최근 수년간 전자기기 산업 기술이 발전함에 따라, 웨어러블(Wearable) 및 스마트 전자기기의 수요가 급증하였다[1-3]. 특히, 기계적 유연성(Flexibility)과 신축성(Stretchability)이 우수한 전자기기를 개발하여 인체에 적용하는 방안을 모색하는 연구가 활발히 이뤄지고 있다[4-6]. 기존의 전자기기들은 전원공급장치로 전기화학 배터리를 주로 사용하였는데, 한정된 용량으로 인해 주기적인 배터리 충전 및 교체가 필요하다는 한계점이 존재한다[7, 8]. 또한, 기존의 벌크형 배터리는 웨어러블 전자기기에 적용하기에 한계가 있어 이를 대체할 수 있는 유연성과 신축성이 뛰어나고 지속 가능한 전원공급장치의 개발이 요구된다[5].
자가 발전이 가능한 웨어러블 전자기기를 구현하기 위한 전략으로, 에너지 하베스팅 기술(Energy harvesting technology)이 기존의 배터리를 대체할 수 있는 차세대 전력원으로 각광받고 있다[9, 10]. 에너지 하베스팅 기술은 자연이나 일상생활에서 버려지는 태양광, 기계적에너지와 열에너지 등을 활용해 전기 에너지로 변환 및 수확하여 에너지를 효율적으로 사용하는 신재생 에너지 기술이다. 그중에서도, 압전 에너지 하베스팅 기술은 소재에 기계적 응력이 인가되었을 때 내부에서 전위차가 형성됨에 따라 전기가 생성되는 현상을 이용한 기술로, 주변에 흔히 발생하는 진동, 충격과 생체 신호 등의 미세한 기계적 에너지로부터 전기적 신호를 생성할 수 있는 기술이다[9, 11]. 이를 기반으로 한 플렉서블(Flexible) 및 스트레쳐블(Stretchable) 압전 에너지 하베스터(Piezoelectric energy harvester)는 미세한 기계적 자극도 전기적 에너지로 변환 가능하여 소형 웨어러블 전자기기 및 생체의료용(Biomedical) 전자기기에 적용 가능하다는 장점이 있다[10, 12].
압전 에너지 하베스터를 개발하기 위해, 압전 효과를 나타내는 다양한 소재들이 연구되어 왔다. BaTiO3, (K,Na)NbO3(KNN)와 Pb(Zr,Ti)O3(PZT) 등의 페로브스카이트(Perovskite) 결정구조를 갖는 압전 세라믹은 압전 특성이 우수하지만, 기계적 취성으로 인해 응용 분야가 한정적이다[13-15]. 특히, PZT와 같은 납계 압전 세라믹은 압전 특성이 우수한 반면, 소재 자체의 독성으로 인해 웨어러블 전자기기에 응용하기 적합하지 않다. 이러한 한계점을 극복하기 위해, 압전 세라믹 소재를 폴리머 기지상(Matrix)에 분산시켜 제작한 압전 복합체에 관한 연구가 활발히 이뤄졌다[10, 16-18]. PDMS(Polydimethylsiloxane)와 Ecoflex rubber같은 폴리머 소재들은 우수한 생체적합성(Biocompatible) 및 성형성을 가지고 있으며 제조 공정이 간단하여 압전 복합체의 기지상으로 각광받고 있다. 특히, Ecoflex는 PDMS에 비해 탄성계수가 낮아 신축성이 우수하고 생분해성(Biodegradable)을 가져 스트레쳐블 압전 복합체의 기상으로 사용하기에 적합하다[6, 19].
본 연구에서는 신축성이 우수한 Ecoflex 폴리머 기지상에 압전 특성이 우수한 BaTiO3 압전나노입자(Nanoparticle)를 분산시켜 스트레쳐블 압전 복합체를 제조하였다[17, 19]. 기존에 PDMS 폴리머를 기지상으로 사용한 소자보다 신축성이 향상되고 신체와 같이 굴곡이 심한 표면에 적용하는 데 용이한 스트레쳐블 압전 센서 어레이를 제작하였다. 간단하고 저비용 공정인 스핀코팅(Spin-coating)을 통해 압전 복합체 후막을 신축성 있는 섬유전극(Textile electrode) 위에 형성하여 소자를 제작하였다. 이때, 하중이 인가되는 채널의 인접 채널에 전달되는 기계적 간섭을 줄여 압전 센서 어레이의 신호 감지 정확도를 향상시키기 위하여 상부 섬유전극을 두 번의 굴곡진 형태(Wavy shape)로 부착하였다. 압전 센서 어레이의 출력 성능을 평가하기 위해 최적화된 측정 장비 시스템을 기반으로 규칙적이고 반복적인 하중을 인가하였으며, 최대 4.3 V의 전압과 5 nA의 전류 신호가 생성되었다. 실제 출력 성능 결과를 뒷받침하기 위해 다중물리(Multiphysics) COMSOL 시뮬레이션 프로그램을 이용한 3차원 유한요소해석(Finite element analysis)을 진행하여 이론적인 성능을 확인하였다. 또한, 압전 센서 어레이에 동시에 하중을 인가할 때, 여러 채널에서 생성되는 신호를 실시간으로 감지하고 구분함으로써, 본 연구에서 개발한 압전 기반의 스트레쳐블 소자가 센서 어레이 적용이 가능함을 확인하였다.
2. 연구 방법
2.1 비납계 BaTiO3 압전나노입자 제조
본 연구에서 사용된 BaTiO3 압전나노입자는 고온에서 확산 반응을 통해 나노입자를 합성하는 고상 반응법을 이용해 제조하였다. 볼 밀링(Ball-milling) 과정을 통해, 고체 상태의 원재료인 BaCO3와 TiO2를 기계적으로 혼합하고 분쇄한 후에 도가니에 넣고 975°C에서 하소(Calcination)을 실시하였다. 하소된 입자를 3 mm 크기의 beads를 이용해 24시간 동안 혼합하여 BaTiO3 압전나노입자를 제조하였다.
2.2 스트레쳐블 압전 복합체 제조
Ecoflex 폴리머 기지상에 BaTiO3 나노입자를 분산시켜 스트레쳐블 압전 복합체를 제작하였다. Ecoflex(Smooth-On, Inc.) A와 B를 1:1로 혼합하고, BaTiO3 나노입자를 20 wt% 비율로 분산시켜 압전 복합체 용액을 제조하였다. BaTiO3 나노입자의 함량이 너무 적으면 압전 성능이 저조하며, 너무 많은 양의 BaTiO3 나노입자는 압전 복합체의 기계적 특성에 악영향을 미칠 수 있어 BaTiO3의 함량을 20 wt%로 설정하였다. 제조된 압전 복합체 용액을 데시게이터(Desiccator)에 넣고 진공펌프를 통해 압전복합체 용액 내에 존재하는 기포를 제거하였다. ITO-coated PET(Indium tin oxide-coated polyethylene terephthalate; 4 cm × 4 cm; thickness, 178 μm) 기판 상에 압전 복합체 용액을 30초간 1,200 rpm으로 스핀코팅한 후 80°C에서 20분간 경화시켜 압전 복합체 막을 형성하였다. 스핀코팅 및 경화 과정을 총 3회 반복하여 PET 상에 두께 약 300 μm의 압전 복합체 후막을 형성하였다. 압전 복합체 내의 전기쌍극자를 동일한 방향으로 정렬하기 위해 폴링 공정을 다음과 같이 수행하였다[9]. 제조된 압전 복합체 상에 임시 상부전극으로 Ti foil(3.5 cm × 3.5 cm)을 부착하고, 전도성 접착제(Silver-based conductive epoxy)를 사용하여 구리 도선과 상·하부 전극을 연결한 후 120°C에서 50 kV/cm의 전기장(Electric field)을 4시간 동안 인가하였다.
2.3 스트레쳐블 압전 복합체 기반의 3 × 3 압전 센서 어레이 제작
PET 기판 상에 Ecoflex를 도포하고 30초간 700 rpm으로 1회 스핀코팅하였다. 상·하부 전극은 신축성있는 은도금 섬유전극을 사용하였다. 코팅된 Ecoflex 상에 하부 섬유전극(0.5 cm × 8 cm)을 1.5 cm 간격으로 3가닥을 부착한 후, 진공오븐을 사용하여 경화시켰다. 폴링 공정을 완료한 압전 복합체를 5 mm × 5 mm 크기로 잘라서 하부 섬유전극 상에 1.5 cm 간격으로 9개를 부착하였다. 압전 복합체 상에 상부 섬유전극(0.5 cm × 9 cm)을 하부 섬유전극과 교차하도록 부착하여, 3 × 3 압전 센서 어레이의 9개 채널을 형성하였다(Fig. 1(a) 참고). 이때, 상부 섬유전극을 두 번의 굴곡진 형태로 부착하였다. 마지막으로, Ecoflex를 Drop-casting하여 압전 센서 어레이를 패키징(Packaging)하였다.
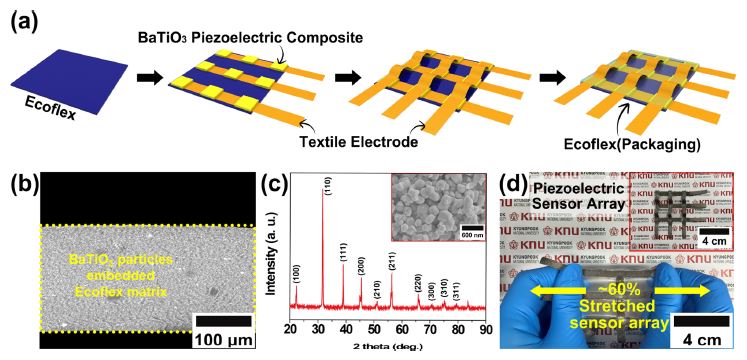
(a) Schematic illustration of the fabrication procedure of the stretchable 3 × 3 piezoelectric sensor array consist of the BaTiO3 nanoparticles and Ecoflex matrix. (b) Cross-sectional SEM image of the piezoelectric composite layer with 20 wt% BaTiO3 nanoparticles. (c) XRD pattern of the piezoelectric BaTiO3 nanoparticles. The inset shows the SEM image of synthesized BaTiO3 nanoparticles. (d) Photograph of the stretchable piezoelectric sensor array with a size of 5 cm × 5 cm stretched by human finger.
2.4 출력 전압 및 전류 신호 측정
제작한 스트레쳐블 압전 센서 어레이의 전기적 출력 성능을 평가하기 위해 자체 제작된 하중인가장치(SnM, Bending Machine System)를 사용하였다. 하중인가장치로 규칙적이고 반복적인 하중을 인가하여 소자에서 생성되는 전압과 전류 신호는 전위계(Electrometer, Keithley 6514/E)로 측정하였다. 다채널 측정장비(Keithley Co., Switch/Multimeter 3706A)를 압전 센서 어레이에 연결하여, 다수의 채널에 하중을 인가할 때 발생하는 전기적 신호를 Imaging program으로 맵핑(Mapping)하여 시각화 하였다. 소자로부터 발생한 출력 신호와 이에 따른 맵핑 결과는 연결된 PC에 실시간으로 기록되었다.
3. 결과 및 고찰
3.1 압전 복합체 기반의 스트레쳐블 3 × 3 압전 센서 어레이
Fig. 1(a)에서 실험 방법에서 설명한 스트레쳐블 3 × 3 압전센서 어레이의 제작 공정의 모식도를 나타내었다. Fig. 1(b)는 주사전자현미경(scanning electron microscopy, SEM)으로 BaTiO3 압전나노입자들이 Ecoflex 기지상에 분산된 압전 복합체의 단면을 촬영한 이미지로, 압전 복합체 후막이 약 300 μm 두께로 균일한 형상임을 보여주고 있다. Fig. 1(c)는 고상 반응법을 통해 제조한 BaTiO3 압전 나노입자의 형상과 X선 회절(X-ray diffraction, XRD) 패턴을 보여주고 있으며, 페로브스카이트 결정구조의 BaTiO3가 평균 350 nm 크기로 잘 합성되었음을 보여주고 있다[20]. (100), (200) 면을 나타내는 피크들에서 피크 분리가 존재하며, 이는 BaTiO3가 정방정계 페로브스카이트 격자 구조임을 나타낸다[21]. Fig. 1(d)는 5 cm × 5 cm 크기로 제작한 스트레쳐블 3 × 3 압전 센서 어레이의 실제 사진이다. 제작된 압전 센서 어레이는 유연하면서도, 약 60%의 높은 인장 변형률을 나타내었다.
3.2 출력 성능 평가, 측정 조건에 따른 성능 평가 및 내구성 테스트 결과
Fig. 2(a)는 압전 센서 어레이의 출력 성능 평가 모식도를 보여주고 있다. 직육면체 형태의 PDMS 블록을 채널 상에 올린 후, 하중인가장치를 통해 PDMS 블록에 규칙적이고 반복적인 하중을 인가하여 압전 센서 어레이의 출력 성능을 평가하였다. 제조된 압전 복합체는 전기쌍극자를 정렬하여 압전성능을 향상시키기 위해 폴링 공정을 수행하였다. 폴링 공정은 50 kV/cm의 전기장을 인가하여 수행하였으며, 50 kV/cm 이상의 전기장을 인가할 경우 압전 복합체 소재 내부에서 절연파괴(Electrical breakdown) 현상이 발생하여 폴링 진행이 불가능하였다[17]. 제작한 압전 센서 어레이는 30 N의 하중을 100 mm/s의 변위속도로 인가했을 때, 최대 4.3 V의 전압 신호와 5 nA의 전류 신호를 생성하였다(Fig. 2(b)). Fig. 2(c)는 압전 센서 어레이에 인가하는 하중의 크기에 따른 출력 전압 값을 나타내고 있다. 인가하는 하중의 크기를 20 N에서 90 N으로 증가시킴에 따라 약 3.2 V에서 6.9 V로 출력 전압이 점점 높아짐을 확인하였다. Fig. 2(d)는 30 N의 하중을 5,000회 반복 인가하였을 때 압전 센서 어레이의 출력 전압 변화를 보여주고 있으며, 출력 전압의 큰 감소 없이 일정하게 유지됨을 통해 제작된 스트레쳐블 압전 센서 어레이가 기계적 안정성이 우수함을 확인하였다.
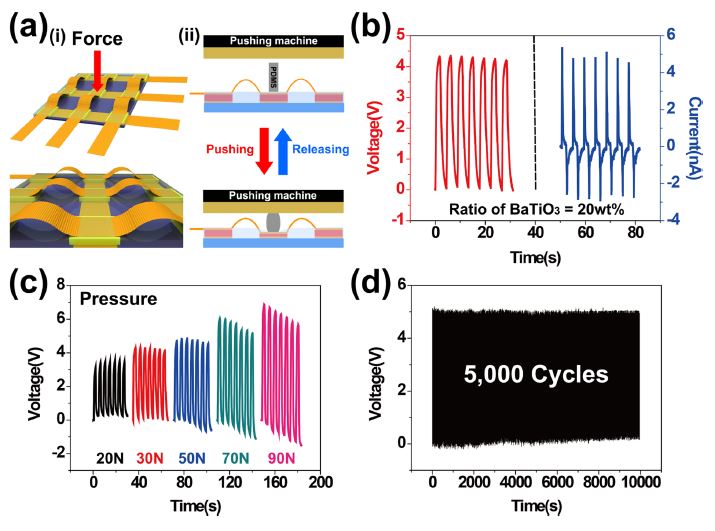
(a) Schematic illustration of measurement process of the piezoelectric sensor array. (b) The measured output voltage and current signals from piezoelectric sensor device under the repeated pushing and releasing motions. (c) Output voltage variation according to the various load conditions. (d) Durability test result showing the stable output performance of the piezoelectric sensor array during 5,000 cycles.
3.3 다중물리 시뮬레이션 수행 및 해석 결과
Ecoflex 폴리머 기지상에 BaTiO3 나노입자가 분산된 압전 복합체 기반의 센서 어레이로부터 생성될 수 있는 최대 전압 신호를 이론적으로 예측하기 위해 다중물리 COMSOL 시뮬레이션 프로그램을 이용한 3차원 유한요소해석을 진행하였다. Fig. 3(a)는 압전 센서 어레이의 출력 성능을 확인하기 위해 시뮬레이션 해석 모델의 모식도를 나타내었다. Fig. 3(b)와 같이, 상·하부 전극 사이에 Ecoflex 기지상을 배치하고, 기지상 내에 압전 세라믹 BaTiO3 구형 입자를 고르게 분산 시킨 간단한 모델을 적용하였다. 하부는 Fixed constraint으로, 상부는 –Z축 방향의 Boundary load로 경계조건으로 설정하여 제작한 모델에 단위 면적당 30 N의 하중을 인가하는 형태로 시뮬레이션 해석을 실시하였다. 시뮬레이션 해석 결과, 상·하부 전극 사이에 약 10 V의 압전 전위차(Piezoelectric potential difference)가 형성되었음을 확인하였다. 본 시뮬레이션을 통해 도출된 해석 결과는 다수의 BaTiO3 압전세라믹 입자가 Ecoflex 폴리머 기지상 내에 일정하게 분산된 모델을 사용하여 얻은 결과로, 모델을 제작할 때 기지상 내에 존재하는 BaTiO3 입자의 수, 크기와 분산된 정도를 실제와 동일하게 맞추는 데는 제약이 있다. 따라서, 모델과 실제 사이에서 출력할 수 있는 성능 차이가 존재한다.
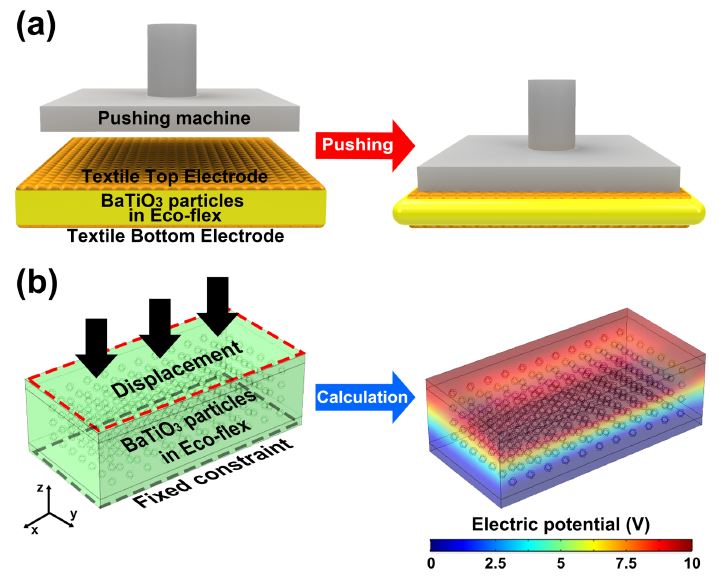
(a) Schematic illustration showing the simulation model of the piezoelectric sensor stressed with compressing deformation. (b) The calculated COMSOL simulation result (right) of geometry (left) with BaTiO3 particles dispersed in Ecoflex matrix. The produced piezoelectric potential difference is indicated by color-codes.
3.4 다채널 측정장비를 통한 출력 전압에 따른 컬러코드 맵핑
하중이 인가되는 채널에 따른 압전 센서 어레이의 출력 신호를 평가하기 위해, 다채널 측정 장비를 기반으로 한 성능 평가시스템을 구축하였다. Fig. 4(a)와 같이, 하중인가장치를 사용하여 압전 센서 어레이의 특정 채널에 하중을 반복적으로 인가하였다. 전위계와 다채널 측정 장비를 기반으로 하여 Fig. 4(b)와 같이 측정 시스템을 구축하였으며, 이를 통해 출력 전압을 측정하고 출력 신호에 따른 맵핑 결과를 실시간으로 기록 및 녹화하였다. Fig. 4(c)는 3 × 3 압전 센서 어레이의 1~9 채널에 해당하는 출력 전압 그래프의 색상과, 하중을 인가하는 채널에서의 전압 신호에 따른 맵핑 결과를 Imaging program으로 시각화한 이미지를 보여주고있다. Fig. 4(d)는 스트레쳐블 3 × 3 압전 센서 어레이의 특정 채널에 하중을 인가할 때, 채널에 따른 전압 신호 그래프를 나타내고 있다. 각 채널에 하중이 인가될 때마다 해당 채널에서 최대 0.45 V의 전압 신호가 생성되었으며, 2개 이상의 채널에 하중을 인가하여도 해당 채널에서 발생한 전기적 신호를 구분하여 감지 가능함을 확인하였다. 하중을 인가하는 채널 외에 다른 채널에서는 전기적 신호가 거의 발생하지 않았음을 실시간으로 도출되는 그래프와 맵핑 이미지를 통해 확인할 수 있다.
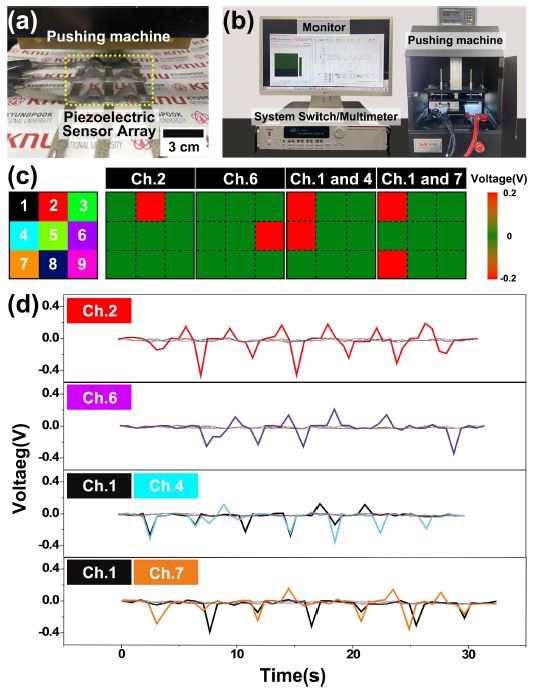
(a) Photographs showing the piezoelectric sensor array under the pushing machine and (b) the measurement system for characterizing the output performance. (c) Color-code mapped image visualized by the imaging program from the detected voltage signals via pushing multiple channels. (d) Generated output voltage signals from the selected channels the piezoelectric sensor array by repeated pushing/releasing stimuli.
3.5 제작된 3 × 3 압전 센서 어레이의 응용
제작된 스트레쳐블 3 × 3 압전 센서 어레이의 실생활 적용가능성을 확인하기 위해 Fig. 5(a)와 같이 키패드에 센서 어레이를 부착하여 응용 실험을 수행하였다. 키패드 숫자 1~9 위에 압전 센서 어레이의 채널 번호와 일치하도록 부착하여 손가락으로 하중을 인가할 때 키패드에서 출력되는 숫자와 맵핑되는 채널 번호의 일치 여부를 확인하였다. Fig. 5(b)는 키패드에 부착된 3 × 3 압전 센서 어레이를 손가락으로 눌러주면서 출력 성능을 측정하는 과정을 보여주고 있다. Fig. 5(c)는 압전 센서 어레이의 각 채널에 해당하는 출력 전압 그래프의 색상과 그에 따른 맵핑 이미지를 보여주고있다. Fig. 5(d)는 키패드 상에 부착된 3 × 3 압전 센서 어레이의 특정 채널을 손가락으로 누를 때, 해당 채널의 출력 전압 그래프를 나타내고 있다. 손가락으로 누른 채널에서 하중 인가에 따른 전압 신호가 감지되었으며, 다른 채널로부터의 간섭 신호 역시 거의 발생하지 않았음을 확인하였다. 키패드로 숫자를 입력함에 따라, Imaging program으로 해당 채널에서 발생하는 전기적 신호를 맵핑하여 시각화하였다. 이를 통해, 간단하고 저렴한 공정으로 제작된 스트레쳐블 3 × 3 압전 센서 어레이가 실시간으로 각 채널에 인가되는 기계적 자극을 감지하고, 감지한 신호를 정확하게 구분 가능하여 상용 전자기기로 적용 가능함을 확인하였다.
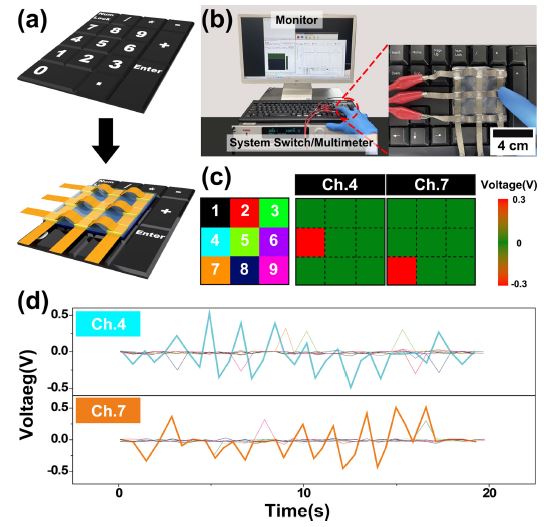
(a) Schematic illustration of application test with the 3 × 3 piezoelectric sensor array attached on keypad. (b) Photographs showing the measurement system and 3 × 3 piezoelectric sensor array attached on keypad. (c) Color-code mapped image visualized by the imaging program from the detected voltage signals via pushing channel. (d) Generated output voltage signals from the selected channel the piezoelectric sensor array by repeated pushing/releasing stimuli.
4. 결 론
본 연구는 BaTiO3 압전 나노입자를 Ecoflex 폴리머 기지상에 분산시켜 스트레쳐블한 압전 복합체를 제작하고, 전극 소재로 신축성이 우수한 은도금 섬유전극을 사용하여 스트레쳐블 압전 센서 어레이를 제작하였다. 하중을 인가하는 채널 외에 인접 채널에 미치는 간섭 영향을 최소화하기 위해서 압전복합체를 단락시키고 섬유전극을 굴곡진 형태로 부착하였다. 하중 인가 장치로 기계적 변형을 인가하여 압전 센서 어레이에서 최대 4.3 V의 전압과 5 nA 전류를 생성하였다. 다중물리 COMSOL 시뮬레이션 해석을 실시하여, Ecoflex를 기지상으로 한 모델을 통해 압전 센서 어레이에 형성된 압전 전위차를 통해 실제 출력 성능을 이론적으로 뒷받침하였다. 또한, 다채널 측정장치를 활용하여 3 × 3 압전 센서 어레이의 채널에 하중을 인가할 때 발생하는 출력 전압을 실시간으로 맵핑하였으며 제작된 압전 센서 어레이를 키패드에 부착하여 사용하는 응용 실험을 통해 스트레쳐블 압전 센서 어레이의 실생활 적용가능성을 확인하였다. 본 연구에서 개발한 압전 센서 어레이는 높은 기계적 안정성과 대면적 형태로의 제작이 가능함을 제시하여 차세대 웨어러블 전자기기 및 스마트 전자기기에 적용할 수 있을 것으로 기대된다.
Acknowledgments
본 연구는 2022년도 정부(과학기술정보통신부)의 재원으로 한국연구재단의 지원(No.2021R1A4A2001658, No.2022R1A2C1003853)을 받아 수행되었습니다.
References
-
L. M. Swallow, J. K. Luo, E. Siores, I. Patel, and D. Dodds, “A piezoelectric fibre composite based energy harvesting device for potential wearable applications”, Smart Mater. Struct., Vol. 17, No. 2, p. 025017, 2008.
[https://doi.org/10.1088/0964-1726/17/2/025017]
-
T. Kim and I. Park, “Skin-interfaced Wearable Biosensors: A Mini-Review”, J. Sens. Sci. Technol., Vol. 31, No. 2, pp. 71-78, 2022.
[https://doi.org/10.46670/JSST.2022.31.2.71]
-
C. Erdmier, J. Hatcher, and M. Lee, “Wearable device implications in the healthcare industry”, J. Med. Eng. Technol., Vol. 40, No. 4, pp. 141-148, 2016.
[https://doi.org/10.3109/03091902.2016.1153738]
-
Y. Jung and H. Cho, “Flexible pressure sensors based on three-dimensional structure for high sensitivity”, J. Sens. Sci. Technol., Vol. 31, No. 3, pp.145-150, 2022.
[https://doi.org/10.46670/JSST.2022.31.3.145]
-
C. K. Jeong, J. Lee, S. Han, J. Ryu, G.-T. Hwang, D. Y. Park, J. H. Park, S. S. Lee, M. Byun, S. H. Ko, and K. J. Lee, “A hyper-stretchable elastic-composite energy harvester”, Adv Mater., Vol. 27, No. 18, pp. 2866-2875, 2015.
[https://doi.org/10.1002/adma.201500367]
-
H.-T. Deng, X.-R. Zhang, Z.-Y. Wang, D.-L. Wen, Y.-Y. Ba, B. Kim, M.-D. Han, H.-X. Zhang, and X.-S. Zhang, “Super-stretchable multi-sensing triboelectric nanogenerator based on liquid conductive composite”, Nano Energy, Vol. 83, p. 103948, 2021.
[https://doi.org/10.1016/j.nanoen.2021.105823]
-
B.-U. Hwang, A. Zabeeb, T. Q. Trung, L. Wen, J. D. Lee, Y.-I. Choi, H.-B. Lee, J. H. Kim, J. G. Han, and N.-E. Lee, “A transparent stretchable sensor for distinguishable detection of touch and pressure by capacitive and piezoresistive signal transduction”, NPG Asia Mater., Vol. 11, No. 1, pp. 1-12, 2019.
[https://doi.org/10.1038/s41427-019-0126-x]
-
G.-T. Hwang, V. Annapureddy, J. H. Han, D. J. Joe, C. Baek, D. Y. Park, D. H. kim, J. H. Park, C. K. Jeong, K.-I. Park, J.-J. Choi, D. K. Kim, J. Ryu, and K. J. Lee, “Self-powered wireless sensor node enabled by an aerosol-deposited PZT flexible energy harvester”, Adv Energy Mater., Vol. 6, No, 13, p.1600237, 2016.
[https://doi.org/10.1002/aenm.201600237]
-
S. S. Ham, G.-J. Lee, D. Y. Hyeon, Y.-G. Kim, Y.-W. Lim, M.-K. Lee, J.-J. Park, G.-T. Hwang, S. Yi, C. K. Jeong, and K.-I. Park, “Kinetic motion sensors based on flexible and lead-free hybrid piezoelectric composite energy harvesters with nanowires-embedded electrodes for detecting articular movements”, Composites Part B, Vol. 212, p.108705, 2021.
[https://doi.org/10.1016/j.compositesb.2021.108705]
- S. Y. Lee and Y. Choi, “Piezoelectric energy harvesting principles and materials”, Polym. Sci. Technol., Vol. 31, No. 6, pp. 484-489, 2020.
-
J. H. Han, K.-I. Park, and C. K. Jeong, “Dual-structured flexible piezoelectric film energy harvesters for effectively integrated performance”, Sensors, Vol. 19, No. 6, p. 1444, 2019.
[https://doi.org/10.3390/s19061444]
-
C. K. Jeong, D. Y. Hyeon, G.-T. Hwang, G.-J. Lee, M.-K. Lee, J.-J. Park, and K.-I. Park, “Nanowire-percolated piezoelectric copolymer-based highly transparent and flexible self-powerd sensors”, J. Mater. Chem. A, Vol. 7, No. 44, pp. 25481-25489, 2019.
[https://doi.org/10.1039/C9TA09864J]
-
D. Y. Hyeon and K.-I. Park, “Piezoelectric flexible energy harvester based on BaTiO3 thin film enabled by exfoliating the Mica substrate”, Energy Technol., Vol. 7, No. 10, p. 1900638, 2019.
[https://doi.org/10.1002/ente.201900638]
-
K.-I. Park, J. H. Son, G.-T. Hwang, C. K. Jeong, J. Ryu, M. Koo, I. Choi, S. H. Lee, M. Byun, Z. L. Wang, and K. J. Lee, “Highly-efficient, flexible piezoelectric PZT thin film nanogenerator on plastic substrates”, Adv. Mater., Vol. 26, No. 16, pp. 2514-2520, 2014.
[https://doi.org/10.1002/adma.201305659]
-
K.-I. Park, S. Xu, Y. Liu, G.-T. Hwang, S.-J. Kang, Z. L. Wang, and K. J. Lee, “Piezoelectric BaTiO3 thin film nanogenerator on plastic substrates”, Nano Lett., Vol. 10, No. 12, pp. 4939-4943, 2010.
[https://doi.org/10.1021/nl102959k]
- S. C. Park, J. H. Lee, Y.-G. Kim, and K.-I. Park, “Flexible energy harvesting device based on hybrid piezoelectric nanocomposite made of lead-free BCTZ ceramic and piezo-polymer”, J. Korean Inst. Electr. Electron. Mater. Eng., Vol. 35, No. 1, pp. 72-79, 2022.
-
Y. J. Kwon, D. Y. Hyeon, and K.-I. Park, “Flexible energy harvester made of organic-inorganic hybrid piezoelectric nanocomposite”, Korean J. Mater. Res., Vol. 29, No. 6, pp. 371-377, 2019.
[https://doi.org/10.3740/MRSK.2019.29.6.371]
-
K.-I. Park, M. Lee, Y. Liu, S. Moon, G.-T. Hwang, G. Zhu, J. E. Kim, S. O. Kim, D. K. Kim, Z. L. Wang, and K. J. Lee, “Flexible nanocomposite generator made of batio3 nanoparticles and graphitic carbons”, Adv. Mater., Vol. 24, No. 22, pp. 2999-3004, 2012.
[https://doi.org/10.1002/adma.201200105]
- W. J. Lee, S.-Y. Park, H. J. Nam, and S.-H. Choa, “Mechanical and optical characteristics of transparent stretchable hybrid substrate using PDMS and ecoflex material”, J. Microelectron. Packag. Soc., Vol. 25, No. 4, pp. 129-135, 2018.
-
D. Y. Hyeon and K.-I. Park, “A comparison study of output performance of organic-inorganic piezoelectric nanocomposite made of piezoelectric/non-piezoelectric polymers and BaTiO3 nanoparticles”, J. Korean Powder Metall. Inst., Vol. 26, No. 2, pp. 119-125, 2019.
[https://doi.org/10.4150/KPMI.2019.26.2.119]
-
I. Pasuk, F. Neatu, S. Neatu, M. Florea, C. M. Istrate, I. Pintilie, and L. Pintilie, “Structural details of BaTiO3 Nano-powders deduced from the anisotropic XRD peak broadening”, Nanomaterials, Vol. 11, No. 5, p. 1121, 2021.
[https://doi.org/10.3390/nano11051121]