
흑연과 CNT 복합체를 압저항체로 하는 PDMS 기반의 바람저항형 유속센서 개발
This is an Open Access article distributed under the terms of the Creative Commons Attribution Non-Commercial License(https://creativecommons.org/licenses/by-nc/3.0/) which permits unrestricted non-commercial use, distribution, and reproduction in any medium, provided the original work is properly cited.
Abstract
In this study, a polydimethylsiloxane (PDMS)-based drag force-type flowmeter was fabricated using a graphite–carbon nanotube (CNT) composite as a piezoresistive material and evaluated. The device was in the form of a cantilever, which was composed of the soft material, PDMS, and fabricated using a mold manufactured by a three-dimensional printer. The cost-effective graphite was mixed with CNTs to serve as a piezoresistive material. The optimal mixing ratio was investigated, and the piezoresistive material formed using a graphite:PDMS:CNT ratio of 1.5:1:0.01 was adopted, which showed a stable output and a high sensitivity. Various forward and backward air flows in the range of 0–10 m/s were measured using the fabricated flowmeter, and both tensile and compression characteristics were evaluated. The measured results showed a stable output, with the resistance change gradually increasing with the air flow rate. Repeatability characteristics were also tested at a repeated air flow of 10 m/s, and the flowmeter responded to the applied air flow well. Consequently, the fabricated device has a high sensitivity and can be used as a flowmeter.
Keywords:
Drag-force type flowmeter, Graphite, CNT, PDMS, Piezoresistive material1. 서 론
최근 사물인터넷(IoT) 기술 및 웨어러블 디바이스에 관한 연구가 활발하게 이루어짐에 따라, 다양한 환경과 구조에 적용가능한 유연 센서에 대한 연구의 중요성이 지속적으로 대두되고있다[1-3]. 그 중에서도 기체나 액체 등 유체의 유속을 측정하는 유속센서는 우리 일상에 가장 밀접하게 연결되어 있는 유체에 대하여 측정하기 때문에 연구 및 상업적으로 다양하게 사용되고 있다. 하지만 상용으로 사용되는 대부분의 유속 센서는 기계식, 터빈식 등이며 이는 구조적으로 고정되어 있어 사용 환경에 대해 한계가 존재한다.
이에 비해, 반도체 공정을 이용한 MEMS 센서의 경우, 이러한 한계를 극복하기 위해 PDMS, 폴리이미드 등 다양한 폴리머 재질을 사용하여 부분적으로 혹은 전체적으로 유연한 형태의 센서를 제작하고 있다. 이는 유속센서에서도 마찬가지이며, 열형[4, 5]뿐만 아니라 바람저항형[6, 7]의 경우에도 많은 연구가 진행되고 있다. 특히, 바람저항형의 경우, 바람에 의한 소자의 휨과 이를 측정하는 압저항으로 크게 이루어지는데, 기존의 열형에 비해 에너지 소모가 작다는 점, 외부에 열영향이 적어 다양한 부분에 적용가능하다는 장점을 가지고 있어 꾸준히 연구가 진행되고 있다[7].
바람저항형 유연 유속센서는 압저항효과를 주로 사용하는데, 이때 많이 사용되는 압저항 물질 중 하나가 바로 CNT, 흑연과 같은 탄소 재료이다[8, 9]. 이 중에서 CNT의 경우 CVD 공정 등 다양한 방법으로 쉽게 제작이 가능하다는 장점을 바탕으로 여러 소자에 적용되어져 왔으며, 전반적으로 압저항 특성이 좋다는 장점을 가지고 있다[10]. 그러나, 가격이 100g당 수십만원 수준으로 상대적으로 비싸다는 점은 상용화를 고려한다면 다소 걸림돌이 될 수 있다[11]. 이에 비해 같은 탄소성분으로 이루어진 흑연의 경우에는 기존의 연구로부터 우수한 압저항 효과를 나타내었을 뿐만 아니라, 가격적 측면에서 100g당 수천 원 수준으로 CNT와 비교하여 1/100 정도로 매우 좋은 가격 경쟁력을 가진다[12]. 따라서, 이러한 흑연이 CNT를 일부 대체할 수 있다고 한다면, 압저항 효과를 충실히 나타내면서도 보다 낮은 가격으로 소자를 제작할 수 있으리라 판단하였다.
이에 본 연구에서는 PDMS로 전체적인 소자를 제작하고, 압저항 물질로 CNT와 흑연을 혼합한 복합물질을 사용하고자 한다. 이를 위해 적절한 센서의 크기를 제시하고, 흑연과 CNT의 비율을 조절하여 공정과 민감도에서 최적의 비율을 찾고자 하였다. 이러한 과정을 통해, PDMS 기반의 CNT, 흑연 복합체를 이용한 바람저항형 유속센서를 제작하였으며, 그 결과값은 아두이노를 통해 확인할 수 있도록 구성하였다. 제작된 소자로 실험한 결과, 본 연구의 소자가 기존 연구와 비교하여 좋은 민감도 특성을 나타나는 것을 확인하였다[4,13-16].
2. 연구 방법
2.1 센서의 설계
본 연구에서 개발한 유연 유속센서는 바람저항형 유속 센서의 일종이다. 일반적으로 바람저항형 유속센서는 바람의 저항을 받기 위해 외팔보 형태로 제작하거나 폴리머 등의 보조적인 구조물을 제작하여 바람방향에 수직으로 위치시키는 구조를 가진다[17, 18]. 이때, 구조물이 유속에 의해 변형되며 이 변형량으로 유량, 유속 등을 측정한다.
외팔보 형태는 PMDS로 제작한다. 압저항체는 흑연과 CNT의 혼합체를 기본으로 하고 PDMS 외팔보 와의 결합성 향상을 위해 PDMS를 첨가하여 제작하였다. 센서에 바람이 가해지는 경우 외팔보의 변형에 의해 압저항체에 저항변화가 발생하여 유속을 측정할 수 있다. 가장 이상적인 센서의 치수와 압저항체 혼합물의 비율을 결정하기 위해 각 인자마다 바람에 대한 저항변화율, 즉 민감도(ΔR/R0)를 비교하여 결정하였다.
2.2 소자 설계
압력에 의한 변위에 따라서 저항변화가 발생하는 효과인 압저항효과를 이용하여 센서를 제작하였다. 외팔보 형태의 PDMS에 흑연과 CNT, PDMS를 혼합해 만든 압저항체를 고정하여 유속에 의한 변위에 대한 저항변화를 측정하였다.
저항은 R=ρL/A으로 표현되고 길이에 비례하므로, 길이가 인장 되면 저항이 증가하고, 길이가 감소하면 저항이 감소한다. Fig. 1은 본 연구에서 제작한 소자에 대한 바람에 대한 변형 원리를 나타낸다. 그림에서 보는 바와 같이, 압저항체가 형성된 면으로 바람이 인가되는 경우에는 휨에 의해 전체적으로 압저항이 늘어나는 효과가 나타나므로 저항이 증가하며, 압저항체가 없는 반대면으로 바람이 인가되는 경우에는 압저항체가 수축되어 저항값이 감소하게 된다.
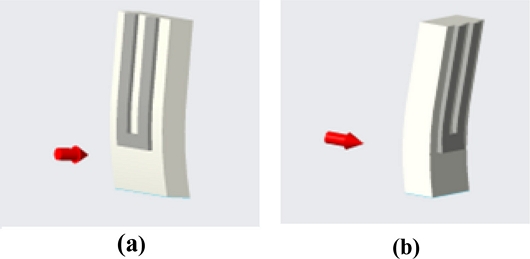
The deformation mechanism of the flowmeter with respect to the air flow direction: (a) forward direction (tensile response) and (b) backward direction (compressive response)
바람 저항형 유속 센서는 외팔보 형태의 구조물을 이용하여 유체 흐름에 대한 저항을 최대화하여 구조물의 휨량으로 소자의 저항변화를 측정한다. 외팔보에 가해지는 힘은 베르누이 방정식을 통해 분산힘(수식1)으로 계산할 수 있으며, 이러한 분산힘 상에서 외팔보의 처짐은 보의 처짐 이론을 바탕으로 계산할 수 있다. (수식2) 외팔보의 처짐량을 기반으로 압저항체의 저항변화를 실험으로 계산하여 최적의 저항변화를 나타내는 길이 및 치수를 선정하고자 하였다.
(1) |
(2) |
여기에서 ρ, v 는 각각 공기의 밀도와 속도를 나타내며, w 는 이를 통해 발생하는 분산힘을 나타낸다. l 은 외팔보의 길이이며, E는 탄성계수로서 기존 문헌을 바탕으로 360 kPa로 설정하였다[19]. 이 수식을 이용하여 계산한 유속에 의한 처짐량을 Fig. 3에 도시하였다. 센서의 두께를 3 mm로 고정하고 길이를 변화시켰을 때 특정 유속의 처짐량 값이다. 이 때, 소자의 길이를 10 mm~20 mm까지 변화시켜가며 그 값을 계산하였다. Fig. 3(b)는 센서의 길이를 10 mm로 고정하고 두께를 변화시켰을 때의 처짐량 값이다. 이 때, 두께는 1 mm~6mm 범위에서 계산을 진행하였다.
3. 실험 방법
3.1 센서 제작
전체적으로 소자는 3D 프린터 몰드를 이용하여 구성하였으며, 소자의 기본 구조인 외팔보 부분은 PDMS와 경화제의 질량비를 10:1로 섞어서 제작하였다[20]. 이때, 소자의 전선 연결 부분의 안정성을 위해 전선 연결부와 유속 측정을 위한 외팔보 부분을 결합한 형태로 몰드를 제작하였다. 압저항 변화를 크게 하기 위해 1 mm 이상의 처짐량을 고려하였으며, 전체적으로 길이 20 mm 폭 15 mm 두께 3 mm로 설정하였다. Fig. 4(a)는 첫번째 몰드로서, 센서의 형태를 그대로 얻고자 제작하였으나, PDMS가 몰드에 함몰된 형태로 구성되어, 경화된 PDMS를 몰드에서 분리하기 어려운 문제점이 발생하였다. 이를 개선하기 위해, Fig. 4(b)와 같이 소자 분리가 용이하도록 몰드 자체를 분리형으로 제작하였다가 최종적으로 전선의 안정성을 고려한 Fig. 4(c) 형태로 변경하였다.
Fig. 5 에서 볼 수 있듯이, 전선을 연결하는 부분의 길이는 10 mm, 폭은 5 mm이며, 소자의 전체적인 두께는 3 mm로 하되 압저항체의 두께를 나타내는 홈의 깊이는 1, 1.5 mm 두 가지로 제작하여 비교 실험을 통해 더 적합한 치수를 선택하였다. 압저항체는 외팔보에 홈을 내어 경화시킨 후 그 홈에 질량비 1.4~1.6:1:0.01=흑연분말:PDMS:CNT의 복합체를 주입하여 제작하였다. 경화시간은 섭씨 90도의 온도에서 40분간 진행하였고, 압저항체의 경화는 진행하지 않았다.
압저항체 제작 시 흑연 (CAS NO.7782-42-5), CNT (MWCNT, CAS NO. 308068-56-6), PDMS의 혼합 비율에 따라 특성이 달라지게 된다. PDMS의 함량이 적어질수록 경화가 되지 않았고, 많아질수록 저항이 측정되지 않았다. 따라서, 적절히 경화가 이루어지면서도 저항측정이 용이한 비율을 선정하였다.
흑연과 CNT의 비율을 결정하는 것 또한 중요한 요소이다. PDMS에 흑연만 존재하는 경우를 기본으로 이와 유사한 저항을 나타내는 CNT 비율을 결정하였으며, 이 때 흑연:CNT의 비율은 150~200:1 수준이였다. 전반적으로 흑연의 용량이 많아지게 되면 초기저항값과 저항변화율에서 편차가 커져 재현성이 떨어지는 문제점이 발생하였다. 이러한 경향은 흑연만을 사용하는 경우 두드러지며, 이 때 초기저항값이 수 kΩ 수준이나 소자에 따라 수백 kΩ~수 kΩ 의 저항값이 발생하여 그 편차가 매우 크게 나타난다. 또한, 제작 후 실험을 진행하는 동안에도 저항값이 수십 kΩ 이상 변동이 생기는 등 안정성에서 문제가 발생하였다. 이러한 부분은 흑연의 파우더 형태 때문으로 생각되며, CNT를 첨가하는 경우 파우더인 흑연의 연결성을 향상시켜 안정성을 높일 것으로 판단하였다.
따라서, 압저항체의 최적 혼합 비율을 찾기 위해 흑연: PDMS: CNT의 비율을 1.4: 1: 0.01, 1.5: 1: 0.01, 1.6: 1: 0.01 로 변화시켜 가며 각 소자의 저항과 저항 변화율을 측정하였다. 이때, 1.5: 1: 0.01의 비율에서 안정도와 민감도가 모두 가장 뛰어나 이 수치를 압저항체의 혼합비율로 결정하였다. 최종적으로 제작된 저항은 1.5 kΩ~2 kΩ 수준으로 측정되었다. 이러한 비율은 앞서 언급한 바와 같이, 가격적인 측면에서도 장점을 지닌다. CNT만을 사용했을 때에 비해, 흑연과 CNT를 혼합하여 제작한 경우 흑연의 부피가 늘어나기는 하나, CNT의 비율이 상대적으로 매우 낮아지기 때문에 압저항체의 가격은 대략 1/3수준으로 낮아짐을 확인할 수 있다.
3.2 풍동 실험 장치
제작된 센서를 아두이노와 유속 실험 장치에 연결하였다. 유속 실험 장치는 Fig. 6에 나타나 있으며, 송풍기에서 유속을 발생시키고 난류의 유속을 Fig. 6(b)의 허니콤 구조를 통해 층류로 변환시켜 센서에 유속을 가하게 된다. 해당 위치에 센서와 대조군으로 쓰게 될 풍속계를 위치시켜 센서의 저항 변화와 풍속계에 측정되는 유속을 비교하였다.
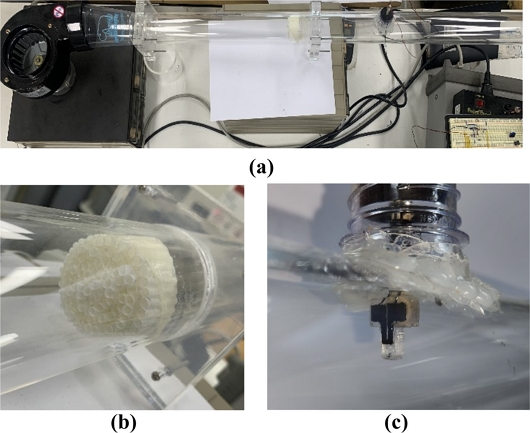
Experimental setup with wind tunnel: (a) overview of test system, (b) honeycomb structure, and (c) sensor in the wind tunnel.
유속에 의해 압저항체가 인장 되는 방향과 압축되는 방향으로 각각 유속실험을 진행하였다. 실험 유속은 2 m/s에서 10 m/s까지 2 m/s씩 올리면서 90초간 저항을 측정하고, 10 m/s에서 90초간 저항을 측정하다가 유속을 1~2초 이내로 급격하게 차단하여 실험하였다. 저항변화율은 저항 변화량과 초기저항을 이용하여 ΔR/R0로 계산하였으며, 실험 시 testo 405i 열선풍속계로 유속을 동시에 측정하여 비교하였다.
4. 실험 결과
4.1 압저항체 두께에 따른 저항변화율
소자의 두께를 결정하기 위해 두께별로 민감도 측정 실험을 진행하였다. Fig. 7 은 PDMS와 흑연만을 혼합하여 소자의 압저항체의 두께에 따라 압저항체의 길이가 늘어나고 줄어드는 방향의 유속으로 저항변화율을 측정한 그래프이다.
그래프에서 확인할 수 있듯이 압저항체의 두께가 1.5 mm보다 1 mm가 되었을 때, 민감도 값이 더 커짐을 알 수 있다. 기본적으로 압저항체의 두께가 얇을수록 압저항체의 위치가 PDMS 외팔보의 중립축과 멀어지게 되고, 이를 통해 전체 변형량 평균이 더 커지는 효과가 발생한다. 따라서, 민감도 차원에서는 압저항체의 두께를 최대한 얇게 제작하는 것이 유리하다. 그러나, 3D 프린터의 해상도 등 제작 여건상, 안정적인 제작을 고려해야 하며, 소형화된 PDMS의 두께와 치수를 유지하며 높은 민감도가 나타도록 PDMS 홈의 깊이를 1 mm로 최종 선택하였다.
4.2 유속 방향에 따른 센서 저항 값 변화
Fig. 8 은 압저항체의 길이가 늘어나는 방향으로 유속과 소자의 저항변화율을 측정한 결과이다. 온도는 섭씨 22.9도 습도는 28%에서 진행하였다. 유속이 증가함에 따라 저항이 함께 증가하는 것을 확인할 수 있으며, 유속이 일정구간 유지되는 경우에는 저항 값의 변화도 이러한 경향성을 따라가는 것을 볼 수 있었다. 단, 최고 유속인 10 m/s에서는 노이즈가 상대적으로 크게 형성되는 것을 확인할 수 있다.
Fig. 9 은 압저항체의 길이가 감소하는 방향으로의 유속과 소자의 저항 측정 결과이다. 이러한 압축방향 실험시에도 인장 방향 유속 측정과 같은 환경에서 실험을 진행하였다. 이 때에는 유속의 증가에 따라 압축이 일어나며, 이에 따라 저항 또한 함께 감소하는 것을 확인할 수 있다. 인장 방향 측정시와 마찬가지로 유속이 일정구간 유지되는 경우에 저항도 이러한 경향성을 따라가는 것을 볼 수 있으며, 인장방향의 유속 측정과 비교하여 상대적으로 적은 노이즈가 관찰되었다.
4.3 흑연, PDMS, CNT 혼합 비율에 따른 민감도 변화
Fig. 10 은 흑연: PDMS: CNT의 비율을 변화시켜가며 그 민감도를 비교한 그래프이다. 그림에서 보는 바와 같이, 흑연 의 비율이 가장 작은 1.4:1:0.01의 비율을 가진 소자보다 1.5:1:0.01의 비율을 가진 소자가 인장과 압축 모두에서 더 민감도가 높은 것을 확인할 수 있다. 전반적으로 흑연 비중이 높아질수록 민감도가 증가하는 경향성을 보이지만, 너무 흑연의 양이 많아지게 되면 오히려 안정성에서 문제가 발생하게 된다. 이는 1.6:1:0.01의 소자에서 확인할 수 있는데, 이 소자의 경우 인장 방향만 특성만 나타나고 압축방향의 특성은 나타나지 않는 모습을 보인다. 또한, 민감도도 오히려 다른 소자에 비해 낮은 모습을 나타냄을 확인할 수 있다. 이러한 점은 파우더 형태의 흑연과 튜브 형태의 CNT가 적정비율에서 서로 연결성이 극대화됨을 나타낸다고 볼 수 있다.
가장 민감도가 높은 1.5:1:0.01의 그래프를 보면, 전체적으로 인장, 압축 모두 민감도가 0.04 수준을 나타낸다. 이러한 민감도는 기존 논문에서 발표된 열형 소자 혹은 바람저항형 소자에 비해 높거나 유사한 민감도를 나타냄을 확인할 수 있다[4,13-16].
4.4 반복 실험 시 저항 변화율 변화
Fig. 11. 은 1.5: 1: 0.01 (흑연: PDMS: CNT)소자를 30초간 안정화 및 30초간 특정 유속(10m/s)으로 반복실험 한 것을 나타낸다. 반복 실험 시 약간의 편차는 있으나, 특정 유속이 유지되는 구간의 길이만큼 저항 또한 일정 시간 유지되는 것을 확인할 수 있다.
Fig. 12(a)는 1.5:1:0.01함량에 두께 1 mm 소자의 압축방향실험을 4회 반복한 결과이다. 동일한 유속 변화에 대해 지속적으로 저항이 감소하고 있으며, 저항변화율 또한 유사한 경향성을 나타나는 것을 확인할 수 있다. 이 실험에서의 데이터들을 평균으로 하여 Fig. 12(b)와 같이 저항변화율-유속으로 매칭시켜 추세선을 통한 관계식을 도출하였다. 이 도출된 추세선 식을 통해 아두이노 코드를 작성하였으며, 이를 통해 유속을 측정할 수 있는 시스템을 구성하였다.
4.5 실제 유속값과 측정 값의 비교
앞 절에서 언급한 추세선 식을 바탕으로 측정회로와 아두이노를 이용한 측정시스템을 구성하였다. 기본적으로 저항의 변화를 측정하는 것이므로, 이러한 저항 변화를 전압으로 측정하여 LCD로 표시하도록 하였다. 이러한 유속을 Fig. 13과 같이 기준 유속계인 testo값과 비교하였다. Testo 유속계의 값은 블루투스를 통해 핸드폰으로 값이 저장되는 형태로서, LCD화면에 측정된 유속값이 실제 유속값인 testo 값과 동일하게 4.21m/s가 출력 되는 것을 확인할 수 있다. 측정기기로 출력한 유속 값은 Fig. 14에서 볼 수 있듯이 실제 유속의 단계적 증가에 따라 증가하는 경향을 가진다.
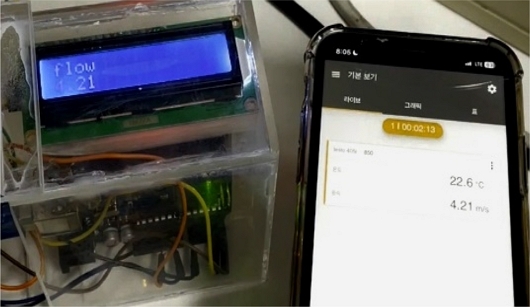
Comparison of measured air flow rate between the fabricated flowmeter (left) and the reference flowmeter (right).
5. 결 론
본 연구에서는 PDMS 기반에 흑연과 CNT를 이용한 압저항체를 적용하여 CNT만을 활용한 소자에 비해 CNT 함량을 줄이고, 이를 통해 제작단가를 절감한 유속센서를 제작할 수 있음을 확인하였다.
기본적으로 간단하고 안정적인 제작을 위해 3D 프린터를 이용한 몰드를 제작하고 이를 통해 소자를 제작하였다. 기본적인 외팔보 구조는 PDMS로 제작하였으며, 외팔보 부분에 위치한 홈에 흑연과 CNT 및 PDMS 복합체를 주입하여 압저항체를 구성하였다. 최적의 흑연, PDMS, CNT 비율을 결정하기 위해, 흑연:PDMS:CNT의 비율을 변경시켜가며 특성을 측정하였다. PDMS 비율이 높을수록 저항값이 증가하였고, 흑연 비율이 높아질수록 재현성이 떨어지는 현상이 발생하였다. 이러한 경향성을 바탕으로, 흑연:PDMS:CNT의 비율을 1.4, 1.5, 1.6:1:0.01로 변경시켜가며 실험한 결과, 1.5:1:0.01인 소자가 측정된 저항이 가장 안정적으로 나타났으며, 압축방향과 인장방향의 유속 모두에 대해 높은 민감도를 나타냄을 확인하였다. 제작한 소자를 이용하여 압저항체 부분에 바람을 받는 인장방향과, 반대인 압축방향에 대해 실험을 진행하였으며, 유속에 따라 인장인 경우 저항이 증가되고, 압축인 경우 저항이 감소하는 경향성을 나타내었다. 10 m/s의 주기적인 유속에서 반복 실험을 진행하여 유속변화에 대해 안정적으로 반응하는 것 또한 확인하였다.
이러한 결과를 바탕으로, CNT와 흑연의 복합체를 사용한 바람저항형 유속센서는 높은 민감도, 저렴한 가격, 그리고 유연성을 이용해 현재 상용 소자들의 한계점을 개선하고 다양한 곳에 적용할 수 있을 것이라 기대된다.
Acknowledgments
본 연구는 정부(교육부)의 재원으로 한국연구재단 기본연구지원사업의 지원으로 수행되었습니다. (NRF- 2017R1D1A1B03030679)
REFERENCES
-
M. Jung, J. Lee, S. K. Vishwanath, O.-S. Kwon, C. W. Ahn, K. Shin, and S. Jeon, “Flexible multimodal sensor inspired by human skin based on hair-type flow, temperature, and pressure,” Flex. Print. Electron., Vol. 5, No. 2, p. 025003, 2020.
[https://doi.org/10.1088/2058-8585/ab8073]
-
A. M. Kamat, X. Zheng, B. Jayawardhana, and A. G. P. Kottapalli, “Bioinspired PDMS-graphene cantilever flow sensors using 3D printing and replica moulding,” Nanotechnol., Vol. 32, No. 9, p. 095501, 2021.
[https://doi.org/10.1088/1361-6528/abcc96]
-
H. Chong, J. Lou, K. M. Bogie, C. A. Zorman, and S. J. A. Majerus, “Vascular Pressure–Flow Measurement Using CB-PDMS Flexible Strain Sensor,” IEEE T. Biomed. Circ. S., Vol. 13, No. 6, pp. 1451-1461, 2019.
[https://doi.org/10.1109/TBCAS.2019.2946519]
-
V. Balakrishnana, T. Dinha, H.-P. Phana, D. V. Dao, and N.-T. Nguyen, “Highly sensitive 3C-SiC on glass based thermal flow sensor realized using MEMS technology,” Sens. Actuators A-Phys., Vol. 279, pp. 293-305, 2018.
[https://doi.org/10.1016/j.sna.2018.06.025]
-
Z. Wang, Z. Yi, R. Tian , M. Qin, Q.-A. Huang , Z.-F. Zhou, and K. Long, “Analysis and Compensation of Benchmark Drift of Micromachined Thermal Wind Sensor Caused by Packaging Asymmetry,” IEEE T. Ind. Electron., Vol. 69, No. 1, pp. 950-959, 2022.
[https://doi.org/10.1109/TIE.2021.3050396]
-
C. M. Park , D. K. Choi , and S. H. Lee, “Study on the Fabrication and Evaluation of the MEMS Based Curved Beam Air Flowmeter for the Vehicle Applications,” J. Sens. Sci. Technol., Vol. 25, No. 2, pp. 116-123, 2016.
[https://doi.org/10.5369/JSST.2016.25.2.116]
-
Y.-H. Wang, C.-Y. Lee, and C.-M. Chiang, “A MEMS-based Air Flow Sensor with a Free-standing Microcantilever Structure,” Sensors, Vol. 7, No 10, pp. 2389-2401, 2007.
[https://doi.org/10.3390/s7102389]
-
L. Chen, G. Chen, and L. Lu, “Piezoresistive Behavior Study on Finger-Sensing Silicone Rubber/Graphite Nanosheet Nanocomposites,” Adv. Funct. Mater., Vol. 17, No. 6, pp. 898–904, 2007.
[https://doi.org/10.1002/adfm.200600519]
-
J. Zhu, W. Song, and R. Huang, “Modulated Pencil-Drawn U-Shaped Piezoresistive Graphite on Compound Fibers for Wind Sensing,” J. Electron. Mater., Vol. 47, No. 11, pp. 6518-6524, 2018.
[https://doi.org/10.1007/s11664-018-6564-3]
-
X. D. Wang, J. C. Wang , S. Biswas, H. Kim, and I. W. Nam, “Mechanical, Electrical, and Piezoresistive Sensing Characteristics of Epoxy-Based Composites Incorporating Hybridized Networks of Carbon Nanotubes, Graphene, Carbon Nanofibers, or Graphite Nanoplatelets,” Sensors, Vol. 20, No. 7, pp. 2094(1)-2094(17), 2020.
[https://doi.org/10.3390/s20072094]
- https://www.thelec.kr/news/articleView.html?idxno=16134, (retrieved on Jan. 2, 2023).
- https://www.komis.or.kr/common/download.do?fid=selfInfoFile&file_seq=383, (retrieved on Jan. 2, 2023).
- B. Seo, H. Hwang, S. Kang, K. Seo, D. Shin, and W. Choi, “Flexible temperature-flow rate dual-parameter fluid sensors using geometric design of thermoelectric materials on PET substrate,” Proc. of the 2017 Spring Conf. of KSME on Therm. Eng., pp. 55-56, 2017.
- H.-S. Park, P.-S. Shin, J.-H. Kim, Y.-M. Baek, and J.-M. Park, “Optimal Manufacturing Conditions and Evaluation of Sensing Performance for Graphite/Paper Sensors for Composite Materials,” Compos. Res., Vol. 31, No. 2, pp. 51-56, 2018.
-
D. Keun Choi and S. H. Lee, “Air Flow Sensor with Corrugation Structure for Low Air Velocity Detection,” J. Sens. Sci. Technol., Vol. 20, No. 6, pp. 393-399, 2011.
[https://doi.org/10.5369/JSST.2011.20.6.393]
- U. Galsanjamts, Study on the Properties of a Drag Force Type Air Flowmeter with respect to Polysilicon Doping Concentrations, M. S. thesis, Seoul National University of Science and Technology, Seoul, 2021.
- Y. U. Lim, Y. J. Cho, and S. H. Lee, “Design and Fabrication of a Frag Force Type air Flowmeter with Poly-Silicon Piezoresistive Layer,” Int. J. Mech. Mechatron. Eng., Vol. 18, No. 4, pp. 89-94, 2018.
-
R. Hagihghi, A. Razmjou, Y. Orooji, M. E. Warkiani, M. Asadnia, “A miniaturized piezoresistive flow sensor for real-time monitoring of intravenous infusion,” J. Biomed. Mater. Res., Vol. 108, No. 2, pp. 568-576, 2020.
[https://doi.org/10.1002/jbm.b.34412]
-
D. Armani, C. Liu, and N. Aluru, “Re-configurable fluid circuits by PDMS elastomer micromachining,” Technical Digest. of IEEE MEMS 99 Conf., Orlando, FL, USA, pp. 222-227, 1999.
[https://doi.org/10.1109/MEMSYS.1999.746817]
-
A. M. Kamat, B. Jayawardhana, and A. G. P. Kottapalli, “PDMS Flow Sensors With Graphene Piezoresistors Using 3D-Printing and Soft Lithography,” Proc. of 2020 IEEE Sens., Rotterdam, Netherlands, pp. 1-4, 2020.
[https://doi.org/10.1109/SENSORS47125.2020.9278740]