
잉크젯 프린팅 기술을 이용한 Ag 전극 균일성 및 발열 센서 연구
This is an Open Access article distributed under the terms of the Creative Commons Attribution Non-Commercial License(https://creativecommons.org/licenses/by-nc/3.0/) which permits unrestricted non-commercial use, distribution, and reproduction in any medium, provided the original work is properly cited.
Abstract
Inkjet printing technology is used to mass-produce displays and electrochemical sensors by dropping tens of pico-liters or less of specific-purpose ink through nozzles, just as ink is sprayed and printed on paper. Unlike the deposition method for vaporizing material in a vacuum, inkjet printing technology can be used for processing even under general atmospheric pressure and has a cost advantage because the material is dissolved in a solvent and used in the form of ink. In addition, because it can only be printed on the desired part, masks are not required. However, a technical shortcoming is the difficulty for commercialization, such as uniformity for forming the thickness and coffee ring effect. As sizes of devices decrease, the need to print electrodes with precision, thinness, and uniformity increases. In this study, we improved the printing and processing conditions to form a homogeneous electrode using Ag ink (DGP-45LT-15C) and applied this for patterning to fabricate a heat sensor. Upon the application of voltage to the heat sensor, the model with an extended width exhibited superior heat performance. However, in terms of sheet resistance, the model yielded an equivalent value of 21.6 Ω/□ compared to the ITO.
Keywords:
Inkjet printing, Uniformity, Ag electrodes, Heating sensor1. 서 론
최근 모바일 디바이스의 소형화로 인하여 미세 패터닝 공정이 요구되고 있다. 특히, 센서 및 디스플레이 응용 분야에서는[1-3] 주로 포토 리소그래피 공정[4]이 사용되고 있으나 원자재 및 장비의 비용 증가로 인하여 제조사들의 부담이 점점 커지고 있어서 기존 포토 리소그래피 공정을 대체할 수 있는 인쇄 전자 산업 및 인쇄 전자 기술[5-7]에 대한 기술들이 관심을 받고 있다 [8]. 그중, 잉크젯 프린팅 기술은 기존의 포토 리소그래피 기술과 비교하였을 때, 빠른 패턴 제작이 가능하며, 공정 과정을 줄여 공정 비용을 절감할 수 있고 또한 원자재의 낭비가 적어 여러 산업에서의 유용한 기술로 평가받고 있다. 잉크젯 프린팅 기술은 원하는 영역에 피코리터(pL)급의 잉크를 프린터 헤드의 노즐을 통해 토출하는 기술이다 [9]. 이는 포토 리소그래피 공정 중 노광 과정에서의 필수적인 마스크와 진공 시스템이 필요하지 않으며, 또한 재료를 용매에 녹여 잉크의 형태로 사용하기 때문에 폐액과 같은 화학적인 오염을 최소화할 수 있어 친환경적이다.
이러한 잉크젯 프린팅 기술에서 핵심적인 부분은 프린터 헤드 기술이다. 프린터 헤드 기술은 헤드를 제어하는 신호의 전압크기, 펄스 폭 등의 조건을 조절함으로써 기판 위에 마이크로(μm)전극을 형성할 수 있게 한다. 기존의 프린팅 기술은 선폭과 두께의 한계로 제한되어 있었으나, 이러한 제약을 극복하기 위해 헤드 제어 기술에 대한 다양한 연구가 진행되고 있다 [10]. 마이크로 단위의 전극을 형성하기 위한 잉크로는 나노 크기의 금속 입자로 구성된 전도성 잉크가 주로 사용되며, 일반적으로 금속은 수백°C에 이르는 녹는 점을 가지고 있지만, 수십 나노단위 크기로 입자를 작게 만들면 낮은 온도에서도 경화가 가능해진다 [11]. 이러한 금속 나노 입자를 분산하고, 용매를 첨가함으로써 잉크로 변환하여 낮은 경화 온도에서도 전극을 형성할 수 있다. 잉크젯 기술과 관련한 지금까지의 연구의 대부분으로 보아, 잉크젯의 기반이 되는 기술인 잉크젯 헤드 기술이나 잉크의 제작과 관련된 기술을 중심으로 연구가 진행되어 왔고, 잉크젯 프린팅 기술의 치명적 단점으로 불리는 커피링 효과(Coffee ring effect)를 제어하는 방안에 대한 연구는 여전히 진행 중이다 [12]. 미세 선폭 전극 형성과 더불어 전기적 특성 확보를 위해서는 균일한 높이를 가지는 전극 형성이 필요하고 커피링 효과를 제어할 수 있는 공정 변수의 영향에 대한 연구가 필요하다. 흔히 균일한 전극 형성을 위해서는 잉크의 물성(표면장력, 점도, 밀도, 용매)의 조절이 필요하거나 프린터 헤드에 인가되는 전압과 waveform을 최적화하는 등 여러 요인들을 제어할 수 있다.
본 연구에서는 위 요인들을 선행 연구로 한 것을 기반으로, 잉크젯 프린팅 후 형성된 액적의 유동에 따라 변화되는 균일성을 분석하기 위해서, 프린팅 후 열처리 공정을 즉시 진행하지 않고 일정 시간 자연적으로 유동하는 과정을 추가함으로써 자연건조 공정 시간에 따른 Ag line의 균일성 변화를 분석하였다. 또한 이를 패턴화하여 발열 센서로 제작하여 인가하는 전압에 따른 온도 및 면저항을 측정하여 선폭에 따른 성능을 분석하였다.
2. 연구 방법
2.1 잉크젯 프린팅
잉크젯 인쇄 기술[13]은 분사 형태에 따라 Continuous 와 Drop-on-Demand (DOD) 방식으로 나뉜다. 먼저 Continuous 방식은 지속적으로 잉크를 토출 시킴으로써 원하는 방향으로 잉크를 분사하기 때문에 인쇄 속도가 빠른 것이 장점이다. Drop-On-Demand방식은 필요한 시간에 잉크를 토출시키는 방식이다. 본 연구에서는 미세한 패턴까지 구현이 가능한 DOD 방식을 채택하였다. 또한 DOD 방식은 잉크 방울을 제어하는 방법에 따라 다시 나누어지는데, 여기에는 열전사 방식(Thermal Drop)과 압전소자 방식(Piezoelectric Drop)이 존재한다. 열전사 방식은 전기에너지로 열을 가하여 노즐 속 용액에 기포가 생기게 하고 온도가 올라가 기포가 커지면서 용액을 밀어내는 원리이며, 압전소자 방식은 전기 에너지를 운동 에너지로 변환하는 압전효과를 이용한 압전소자에 전달하는 전기 신호에 따라 잉크를 제어하는 원리이다. 후자의 경우 전자와 다르게 열을 가하지 않아 용액이 변질될 우려가 없고 정밀한 제어가 가능하기에 압전소자 방식을 채택하였다. 압전소자 방식에서는 소자의 동작 모드에 따라 네 가지로 분류한다: Squeeze(압착), Bend(굽힘), Push(밀어내기), 그리고 Shear(전단). 본 연구에 사용된 Squeeze 모드는 잉크를 양쪽에서 압력을 가하며 쥐어짜는 방식을 가리키고, Bend 모드는 잉크 챔버의 한 쪽 벽을 굽히는 방식을 말한다. Push 또는 Bump 모드는 잉크 챔버의 벽을 밀어내어 잉크를 토출시키는 방식이며, Shear모드는 전단 변형을 통해 잉크를 토출시키는 방식을 의미한다. 잉크젯 프린팅 공정에 사용된 잉크는 나노 신소재(ANP)에서 구매한 실버 나노 잉크(DGP-40LT-15C, Table 1)를 사용하였고, 이것을 2.4pL Samba 카트리지에 채워 후지필름사의 잉크젯 프린팅 장비(Dimatix DMP-2831)에 결합하여 인쇄를 진행하였다.
2.2 마이크로 전극 제작
Ag 잉크를 프린팅 할 기판은 가로와 세로가 25 mm×25 mm, 두께가 0.7 mm인 일반 유리기판을 사용하였으며, 오염물질을 세정하기 위한 목적으로 acetone과 isopropyl alcohol을 사용하여 각각 10분씩 초음파 세척하였다. 그 후, 100°C 오븐에서 약30분간 건조를 진행하여 수분을 제거한 후 사용하였다. 잉크를 프린팅 하고 생성된 액적의 간격을 의미하는Drop space(DS)의 경우 35 DPI (Dots per inch)의 간격을 유지한 채로 인쇄하였고 카트리지의 온도는 27.8°C, 습도는 50%의 환경에서 진행하였다. 인쇄가 끝난 후 자연 건조 시간에 따른 Ag line의 균일성 변화를 확인하기 위해 1~5분까지 1분 간격으로 온도 22°C, 습도 35%의 환경에서 자연 건조를 시킨 후, 120°C에서 5분 열처리를 진행하였다.
2.3 발열 센서 제작
원하는 도면을 비트맵 이미지로 변환하여 프린터 소프트웨어에 입력하여 인쇄할 수 있다. 발열 센서를 제작하기 위해 줄 발열 현상을 유도하는 격자 구조 패턴을 제작하였다. 패턴 설계시 발열 센서의 발열 성능 차이를 확인하기 위해 선폭의 두께를 다르게 하여 격자 사이의 빈 공간의 크기를 조절하였다. 모든 센서의 프린팅 조건은 균일하게 형성된 마이크로 전극 제작조건과 동일하게 진행하였다. (프린팅 후 5분의 자연건조 후 120°C에서 5분 열처리)
2.4 분석 및 성능평가
전극의 균일성을 분석하기 위해 3D Profiler(NV-1800, Nanosystem)와 광학현미경 (BX-53F2, OLYMPUS)을 사용하였고, 발열 센서의 발열 성능을 분석하기 위해 센서 양단에 전압을 가하는 용도로 Source meter(KEITHLEY-2400)를 사용하고 발열을 측정하는 용도로 적외선 카메라(T620, FLIR)를 사용하였다.
3. 결과 및 고찰
3.1 마이크로 전극의 자연건조 특성
마이크로 전극 인쇄 시, 자연건조 시간이 Ag line의 균일성 변화에 미치는 영향을 분석하기 위해 Ag ink를 유리기판 위에 형성한 뒤, 즉시 열처리하지 않고 자연적으로 건조하는 시간을 부여하여 건조 시간에 따른 Ag line의 균일성 변화를 분석하였다.
먼저 잉크의 토출을 확인하기 위해 실버 잉크에 적절한 파형을 입력하여 테스트를 진행하였다. Fig. 2(a)는 Ag ink를 실제 잉크젯 프린팅을 진행할 때, 사용한 전압 펄스 파형이다. 전압 조건을 30 V로 2.176 μs 동안 인가하였으며, Fig 2.(b)는 (a) 조건을 이용한 잉크의 실제 토출한 이미지다. 10 μs의 간격으로 촬영한 이미지로, 실버 잉크가 안정적으로 토출되고 있음을 확인할 수 있다. 이러한 조건으로 Ag line을 프린팅 하였으며, 휘발성을 가지는 용매에 대해 자연건조 시, Ag line의 형상을 확인하기 위하여 1분부터 30분까지 자연건조 후 열처리를 통해 경화시킨 후 각각 분석 비교를 하였다 [14]. Fig. 3(a)~(e)는 자연건조 시간에 따른 Ag line의 형성 모양을 비교하기 위해 3차원 형상을 측정한 이미지를 나타낸다. Fig. 3(f)는 Ag line의 선폭과 높이 데이터를 입력하여 형성 모양을 나타낸 그래프이다. 공통적으로 Ag line의 선폭은 50 μm 로, Ag line의 높이는 100 nm정도로 형성되었다. Fig. 3(a)는 Ag line의 자연 건조 시간을 1분간 한 샘플이며, 건조된 형상을 보면 가운데 부분이 아래로 파인 U자 형태를 가지지만, 자연건조 시간이 증가하면 할수록 가운데 높이가 점점 증가하여 Fig. 3(e)의 경우처럼30분 건조를 진행하면 위로 솟아 있는 형상을 확인할 수 있다. 그러나 Fig. 3(b)에서처럼 자연건조를 5분 진행할 경우, Ag line의 상단부분이 평탄화되어 박막의 균일성이 향상되는 것을 확인하였다. 인쇄 전극의 균일성으로 보아 5분 자연 건조 샘플의 상단부 높이의 경우 ±1.5 nm 정도의 균일성을 가지며, 전통적인 진공 열 증착 공정에서 표면 단차 0.8 nm~ 7.5 nm의 값을 가지는 Ag film과 비교하여 유사하게 형성되었음을 확인하였다 [15]. 자연 건조 공정이 토출된 잉크 액적의 유동 속도에 미치는 영향을 분석하기 위해 Ag line 인쇄 후 자연건조를 진행하고 열처리 공정 없이 곧바로 3차원 형상을 측정하여 Ag line의 높이 변화량을 분석 진행하였다. 그 후 선폭과 높이를 건조 시간에 따른 잉크 높이 변화량을 Fig. 4에 나타내었다. 일반적으로 자연 건조 시간이 증가하게 되면, 증발이 진행되기 때문에 잉크 높이는 감소하게 되지만, 5분 이후 부터의 Ag line의 높이 변화는 점차 감소하는 경향을 보인다. 이는 잉크의 유동속도가 감소하여 증발속도가 느려짐을 확인할 수 있다. 잉크젯 프린팅 후 형성된 액적은 잉크가 유동하려는 특징의 잉크 유동 속도와, 잉크가 증발하려는 특징의 잉크 증발 속도에 의해서 액적의 모양이 결정된다. 만약 잉크의 유동속도가 증발속도보다 빠를 경우 표면적이 넓어지는 엣지 쪽으로의 용질이 더 빠르게 이동하기 때문에, U자형 모양을 가지게 된다. 반대로 잉크의 유동속도가 증발속도보다 느릴 경우 용질이 엣지 쪽으로 이동하기 전에 증발이 되기 때문에, 가운데 부분이 올라와 있는 모양이 형성된다. 균일한 모양을 형성하기 위해서는 잉크의 유동속도와 증발속도를 최대한 같도록 제어해야 할 것이다 (Table 2) [16-19].
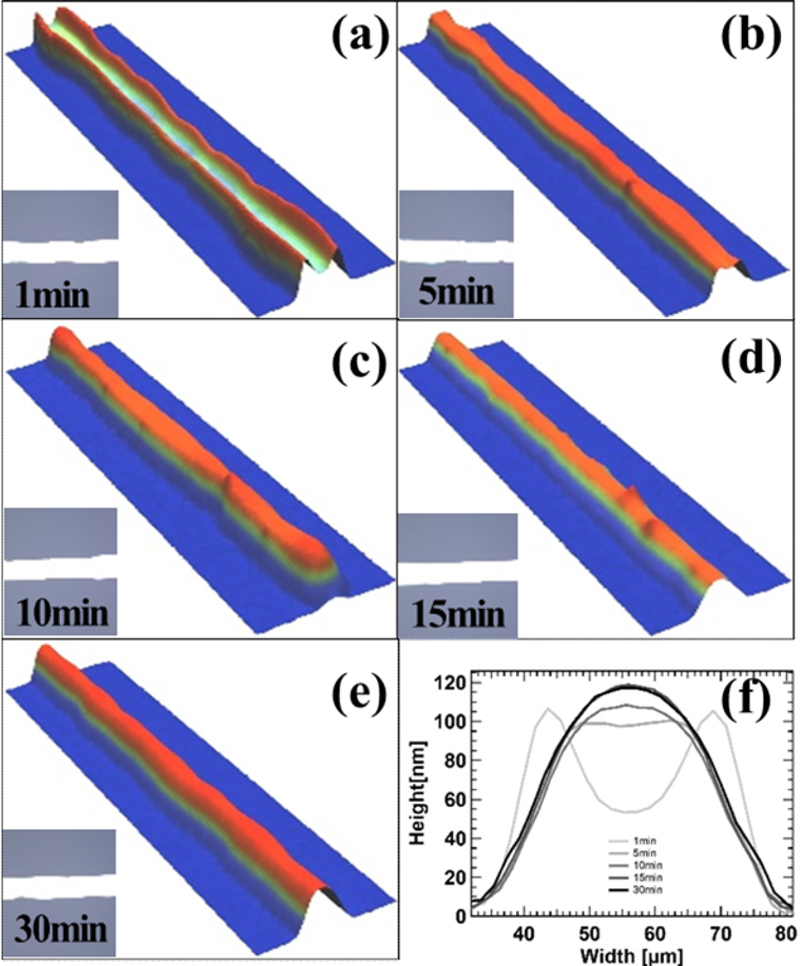
Morphological Changes of Ag line Over Time During Natural Drying (a) 1 min, (b) 5 min, (c) 10 min, (d) 15 min, (e) 30 min, (f) graph of 1 to 30 min.
실버 잉크 [20]는 나노 실버 입자와 용매(Ethyl- alcohol, IPA)가 섞여 있는 형태인데, 이 용매들은 나노 실버 입자에 비해 유동속도가 빠르다. 인쇄 직후 이 용매들이 점점 증발하면서 잉크의 높이가 감소함에 따라 유동속도도 감소되는 것이다. 감소된 유동속도가 증발 속도와 같아지게 되는 자연건조 시간 5분 조건 이후, 열처리를 통해 경화시켜 균일한 Ag line을 형성할 수 있었다. 따라서 Ag 잉크의 유동속도를 제어하기 위해서 자연건조 공정의 변화를 통해 균일한 Ag line을 형성할 수 있음을 확인하였으며, 이 결과는 잉크의 증발속도와 유동속도가 비슷해지는 시점이기 때문이다.
3.2 발열 센서 성능 측정
자연건조 공정을 적용하였을 때, 전극선이 균일하게 형성되는 조건을 활용하여, 균일한 마이크로 전극을 격자 구조로 패터닝하여 발열 센서를 제작하였다. Ag line의 선폭 차이에 따른 성능을 확인하기 위해 패터닝 격자의 선폭을 각각 50 μm, 100 μm, 250 μm, 500 μm로 제작하였다 [21-23]. 성능 평가를 위해 양단에 전압을0.5 V~1.5 V까지 0.5 V 간격으로 전압을 인가하였고, 전압 인가 후 발열 온도가 포화되는1분 경과한 시점에서 적외선 카메라로 온도를 측정하였으며. 선폭에 따른 발열 성능 차이를 분석하였다. 측정 방법은 Fig. 5를 통해 나타내었다. 전압을 인가하면 Ag line따라 이동하는 전자와 Ag line을 구성하고 있는 원자 이온 사이에 충돌이 발생하고, 이 충돌 에너지가 열로 나타나는 줄(Joule) 현상으로 [24]센서에 발열이 일어나며, 인가 전압이 증가하면 할수록 더 높은 열이 발생하는 것을 확인하였다. Fig. 6 에는 적외선 카메라로 히터 센서의 발열을 촬영한 모습을 선폭 별로 나타낸 그림이다. 100 μm 샘플을 제외하고, 발열되는 영역으로 보아 패터닝된 부분이 전면적으로 발열되는 것이 아니라 특정 부분에서 발열이 이루어지는 것을 확인할 수 있다. 이는 저항이 가장 낮은 부분으로 전류가 흘러, 전류가 흐르지 않는 부분은 줄효과가 발생하지 않기 때문이다. 전압에 따른 발열 온도 측정 결과를 Fig. 5를 통해 나타내었다. Fig. 5(a)~(d)의 발열 이미지를 보면 100 μm 선폭이 가장 이상적인, 전면 발열을 이루는 모습을 확인할 수 있다 [25]. 다음으로 50 μm 선폭은 특정 영역에서 발열이 이루어지는 것을 확인할 수 있었고 250 μm 선폭은 특전 라인을 따라 발열이 이루어지는 것을 확인할 수 있었다. 마지막으로 500 μm 선폭에서는 발열이 전압 인가를 위한 패드 부분에서만 발열이 이루어져 패터닝 영역에서 동작하지 않는 것을 확인하였다. Fig. 5(e)는 전압을 0.5 V~1.5 V로 0.5 V간격으로 전압을 인가할 때 패터닝 샘플의 선폭에 따른 온도 변화를 나타낸 그래프이다. 균일하게 발열하는 100 μm 선폭 샘플의 경우 비교적 높은 발열이 이루어지고 50 μm, 250 μm 그리고 500 μm 순으로 발열 성능이 떨어지는 것을 확인할 수 있다. Fig. 6은 선폭을 다르게 한 센서들의 성능 차이의 원인을 확인하기 위해 패터닝 샘플을 현미경으로 촬영한 이미지를 나타낸다. 100 μm 선폭의 Ag line이 가장 균일하게 인쇄된 것을 확인할 수 있고 다음으로는 50 μm, 250 μm, 그리고 500 μm 순으로 현미경 이미지 상으로 인쇄 균일도가 100 μm 선폭에 비해 떨어지는 것을 확인하였다. 따라서 100 μm 선폭에서 최대 발열 면적과 높은 발열 효율을 가지고, 인쇄 전극의 균일도가 향상됨에 따라 히터 센서의 발열 성능 또한 향상되는 것을 확인할 수 있었다.
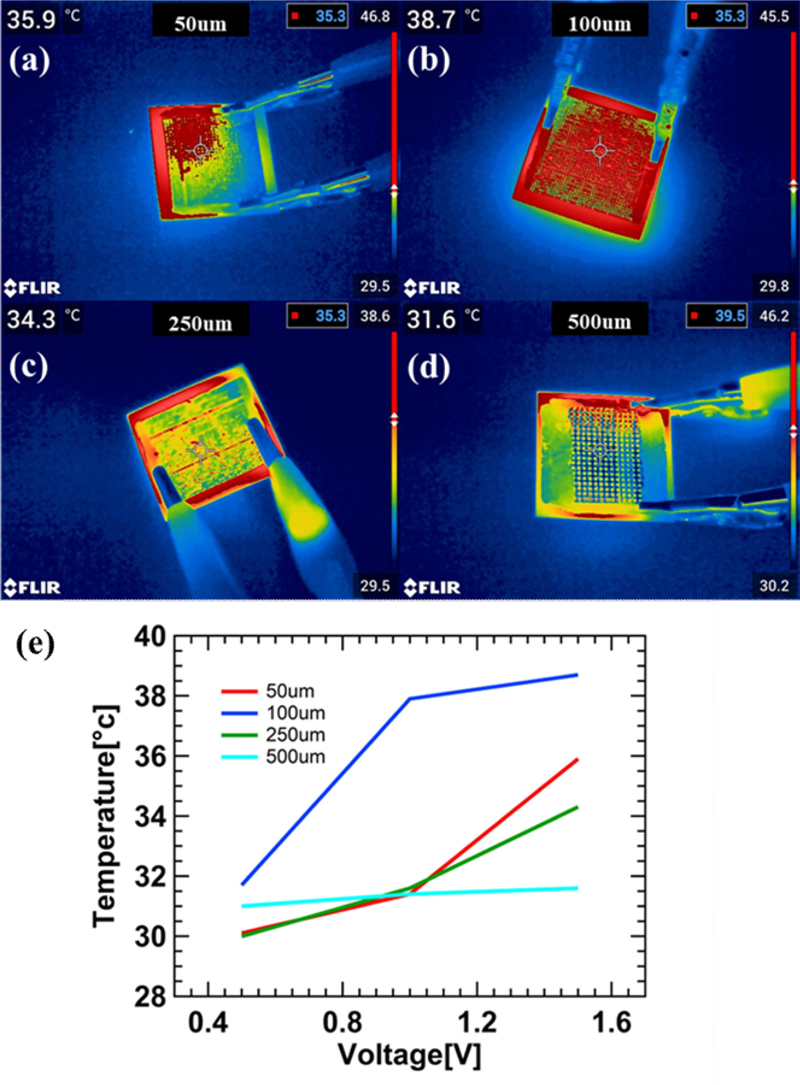
Images of Ag Patterning Heater Sensor Measured by Infrared Camera at Different Line Widths (a) 50 μm, (b) 100 μm, (c) 250 μm, (d) 500 μm, and (e) graph of heater sensor properties according to Ag line widths.
4. 결 론
본 연구에서는 잉크젯 프린팅 공정 기반 Ag 잉크의 균일한 전극선을 형성하기 위해서, 잉크의 유동속도를 제어하는 방법으로 자연건조 공정 시간의 변화를 도입하였고, 이에 따른 Ag line의 균일성 변화에 대한 연구를 진행하였다. 자연건조 시간을 부여할 시, Ag line의 형상이 변화하는 것을 확인하였으며, 특히 Ag line의 가운데 높이가 변화하여 5분의 자연건조 공정을 거칠 경우 비교적 균일한 Ag line을 형성시킬 수 있었다. 이는 프린팅된 Ag 잉크의 유동속도와 증발속도가 일치되는 시점이기 때문이다. 또한 Ag line을 선폭이 각기 다른 격자 구조로 패터닝하여 발열 센서를 제작한 결과, Ag line의 균일성이 향상됨에 따라 센서의 발열 면적의 균일도, 발열 성능이 향상되는 것을 확인하였다. 특히 100 μm 선폭의 경우 Ag line이 다른 선폭들 보다 균일하게 형성되어 우수한 발열 면적과 발열 성능을 가지는 센서를 제작할 수 있었다. 본 연구를 바탕으로 잉크젯 프린팅 공정에서 잉크의 유동속도를 제어하는 방법론은 프린팅된 액적 또는 선의 균일성을 향상시킬 수 있는 기술로 활용될 수 있을 것이다. 다만 자연 건조 공정 시, 대기 환경을 제어하기 어려우므로 다양한 변수에 직면할 수 있다. 신뢰도를 증가시키기 위해 자연 건조 공정을 특정 조건에서 진행할 수 있는 환경이 필요하다. 마이크로 전극의 균일성과 전기적 특성이 개선된다면, 다양한 반도체 및 디스플레이 분야에 광범위하게 활용될 것으로 기대한다. 또한 발열 센서의 경우 패턴의 선 간격을 조정하여 인쇄하여 투명하게 제작하거나, 특정 패턴을 설계하여 발열면적 및 발열 효율을 향상시킬 수 있을 것으로 기대한다. 또한 잠재적인 응용 분야로 의료 기술에서 코로나 바이러스 PCR 검출기의 시료를 열 반응시키는데 사용되거나, 기후 조건의 변화로 인해 발생하는 성에나 서리를 제거하는 데 사용되어 항공기나 차량의 안전 문제에도 응용될 것으로 기대된다 [26-27].
Acknowledgments
이 성과는 정부(과학기술정보통신부)의 재원으로 한국연구재단의 지원을 받아 수행된 연구이다(No. 2022 R1F1A1074746, RS-2023-00222166). 또한 SDC-경상국립대학교 산학협력 센터 과제의 지원을 받아 수행한 연구이다.
REFERENCES
-
H. Kudo, T. Sawada, E. Kazawa, H. Yoshida, Y. Iwasaki, and K. Mitsubayashi, “A flexible and wearable glucose sensor based on functional polymers with Soft-MEMS techniques”, Biosens. Bioelectron., Vol. 22, No. 4, pp. 558-562, 2006.
[https://doi.org/10.1016/j.bios.2006.05.006]
- I. Manunza, A. Sulis, and A. Bonfiglio, “Organic semiconductor field effect transistors for unconventional applications: flexible sensors and wearable devices”, Proc. of International Workshop on Wearable and Implantable Body Sensor Networks, pp. 3-5, Cambridge, USA, 2006.
- H. Takao, M. Miyasak, H. Hara, A. Miyazaki, T. Kodaira, S. W. B. Tam, S. Inoue, and T. Shimoda, “Flexible semiconductor devices: Fingerprint sensor and electrophoretic display on plastic”, Proc. of IEEE conf. on the 34th European Solid-State Device Research, pp. 309-312, Leuven, Belgium, 2004.
-
L. F. Thompson, “An Introduction to Lithography”, American chemical society, Vol. 1, pp1-13, 1983.
[https://doi.org/10.1021/bk-1983-0219.ch001]
-
K. Jain, M. Klosner, M. Zemel, and S. Raghunandan, “Flexible Electronics and Displays: High-Resolution, Roll-to-Roll, Projection Lithography and Photoablation Processing Technologies for High-Throughput Production”, Proc. IEEE, Vol. 93, No. 8, pp. 1500-1510, 2005.
[https://doi.org/10.1109/JPROC.2005.851505]
-
J. P. Metters, R. O. Kadara, and C. E. Banks, “New directions in screen printed electroanalytical sensors: an overview of recent developments”, The Royal Society of Chemistry, Vol. 136, pp. 1067-1076, 2011.
[https://doi.org/10.1039/c0an00894j]
-
G. F. Trindade, F. Wang, J. Im, Y. He, A. Balogh, D. Scurr, I. Gilmore, M. Tiddia, E. Saleh, D. Pervan, L. Turyanska, C. J. Tuck, R. Wildman, R. Hague, and C. J. Roberts, “Residual polymer stabiliser causes anisotropic electrical conductivity during inkjet printing of metal nanoparticles”, Commun. Mater., Vol. 2, No. 47, pp. 1-10, 2021.
[https://doi.org/10.1038/s43246-021-00151-0]
-
C. W. Sele, T. Von Werne, R. H. Friend, and H. Sirringhaus, “Lithography-Free, Self-Aligned Inkjet Printing with Sub-Hundred-Nanometer Resolution”, Adv. Mater., Vol. 17, No. 8, pp. 997-1001, 2005.
[https://doi.org/10.1002/adma.200401285]
-
S. Khan, L. Lorenzelli, and R. S. Dahiya, “Technologies for Printing Sensors and Electronics Over Large Flexible Substrates: A Review”, IEEE Sens. J., Vol. 15, No. 6, pp. 3164-3185, 2015.
[https://doi.org/10.1109/JSEN.2014.2375203]
-
O. Kiefer and J. Breitkreutz, “Comparative investigations on key factors and print head designs for pharmaceutical inkjet printing”, Int. J. Pharm., Vol. 586, pp. 119561(1)-119561(11), 2020.
[https://doi.org/10.1016/j.ijpharm.2020.119561]
-
A. Kosmala, R. Wright, Q. Zhang, and P. Kirby, “Synthesis of silver nano particles and fabrication of aqueous Ag inks for inkjet printing”, Mater. Chem. Phys., Vol. 129, No. 3, pp. 1075-1080, 2011.
[https://doi.org/10.1016/j.matchemphys.2011.05.064]
-
D. Soltman and V. Subramanian, “Inkjet-Printed Line Morphologies and Temperature Control of the Coffee Ring Effect”, Langmuir, Vol. 24, No. 5, pp. 2224-2231, 2011.
[https://doi.org/10.1021/la7026847]
-
Herman Wijshoff, “The dynamics of the piezo inkjet printhead operation”, Phys. Rep., Vol. 491, No. 4-5, pp. 77-177, 2010.
[https://doi.org/10.1016/j.physrep.2010.03.003]
-
C. Kim, J. H. Park, J. Ko, S. Lee, R. G. Kwon, S. Lee, H. Lee, J. Y. Kim, and H.-J. Song, “Room temperature processed protective layer for printed silver electrodes”, RSC Adv., Vol. 13, No. 30, pp. 20557-20564, 2023.
[https://doi.org/10.1039/D3RA02212A]
-
Y. Zhao, X. Liu, D. Y. Lei, and Y. Chai, “Effects of surface roughness of Ag thin films on surface-enhanced Raman spectroscopy of graphene: spatial nonlocality and physisorption strain”, Nanoscale, Vol. 6 pp. 1311-1317, 2014.
[https://doi.org/10.1039/C3NR05303B]
-
R. Tao, Z. Fang, J. Zhang, H. Ning, J. Chen, C. Yang, Y. Zhou, R. Yao, Y. Song, and J. Peng, “Capillary force induced air film for self-aligned short channel: pushing the limits of inkjet printing”, Soft Matter, Vol. 14, No. 46, pp. 9402-9410, 2018.
[https://doi.org/10.1039/C8SM01984C]
-
M. Singh, H. M. Haverinen, P. Dhagat, and G. E. Jabbour, “Inkjet Printing-Process and Its Applications”, Adv. Mater., Vol. 22, No. 6, pp. 673-685, 2010.
[https://doi.org/10.1002/adma.200901141]
-
H. Hu and R. G. Larson, “Analysis of the Microfluid Flow in an Evaporating Sessile Droplet”, Langmuir, Vol. 21, No. 9, pp. 3963-3971, 2005.
[https://doi.org/10.1021/la047528s]
-
E. Mayoral and A. G. Goicochea, “Modeling the temperature dependent interfacial tension between organic solvents and water using dissipative particle dynamics”, J. Chem. Phys., Vol. 138, No. 9, pp. 094703(1)-094703(7), 2013.
[https://doi.org/10.1063/1.4793742]
-
E. Halonen, T. Viiru, K. Östman, A. L. Cabezas, and M. Mäntysalo, “Oven Sintering Process Optimization for Inkjet-Printed Ag Nanoparticle Ink”, IEEE Trans. Compon. Packaging. Manuf. Technol., Vol. 3, No. 2, pp. 350-356, 2013.
[https://doi.org/10.1109/TCPMT.2012.2226458]
-
Q. Huang, K. N. Al-Milaji, and H. Zhao, “Inkjet Printing of Silver Nanowires for Stretchable Heaters”, ACS Appl. Nano Mater., Vol. 1, No. 9, pp. 4528-4536, 2018.
[https://doi.org/10.1021/acsanm.8b00830]
-
D. Barmpakos, V. Belessi, N. Xanthopoulos, C. A. Krontiras, and G. Kaltsas, “Flexible Inkjet-Printed Heaters Utilizing Graphene-Based Inks”, Sensors, Vol. 22, No. 3, pp. 1173(1)-1173(10), 2022.
[https://doi.org/10.3390/s22031173]
-
N. Zhang, C. Huang, S. Wan, L. Kang, M. Hu, Y. Zhang, X. Wu, and J. Zhang, “A Novel Flexible Silver Heater Fabricated by a Solution-Based Polyimide Metalization and Inkjet-Printed Carbon Masking Technique”, ACS Appl. Electron. Mater., Vol. 1, No. 6, pp. 928-935, 2019.
[https://doi.org/10.1021/acsaelm.9b00109]
-
D. Erickson, D. Sinton, and D. Li, “Joule heating and heat transfer in poly(dimethylsiloxane) microfluidic systems”, Lab. Chip, Vol. 3, pp. 141-149, 2003.
[https://doi.org/10.1039/b306158b]
-
H. I. Mohammed, P. Talebizadehsardari, J. M. Mahdi, A. Arshad, A. Sciacovelli, and D. Giddings, “Improved melting of latent heat storage via porous medium and uniform Joule heat generation”, J. Energy Storage, Vol. 31, pp. 101747(1)-101747(11), 2003.
[https://doi.org/10.1016/j.est.2020.101747]
-
K. Kim, B. Lee, J. H. Park, J.-H. Park, K. J. Lee, T. J. Kwak, T. Son, Y.-B. Shin, H. Im, and M.-G. Kim, “Rapid PCR kit: lateral flow paper strip with Joule heater for SARS-CoV-2 detection”, Mater. Horiz., Vol. 10, pp. 1697-1704, 2023.
[https://doi.org/10.1039/D2MH01267G]
-
R. Xu, B. Sun, X. Han, W. Hong, J. Xu, H. Zhu, Z. Fu, Y. Xu, X. Sun, and K. Qian, “High-Performance Flexible Transparent Electrical Heater Based on a robust Ordered Ag Nanowire Micromesh Conductor”, ACS Appl. Electron. Mater., Vol. 4, pp. 1776-1783, 2022.
[https://doi.org/10.1021/acsaelm.2c00029]