
BT50용 스핀들 공구 파지력 검사를 위한 힘센서 개발
This is an Open Access article distributed under the terms of the Creative Commons Attribution Non-Commercial License(https://creativecommons.org/licenses/by-nc/3.0/) which permits unrestricted non-commercial use, distribution, and reproduction in any medium, provided the original work is properly cited.
Abstract
In this paper, we describe the development of a force sensor to measure the tool gripping force of the BT50 spindle. The force sensor for a BT50 must be installed inside the gripping force tester; hence, it must be of an appropriate size and have a rated capacity suitable for measuring the gripping force. So, the structure of the force sensor for BT50 was modeled, the size of the sensing part was determined by structural analysis, and the force sensor was manufactured by attaching a strain gauge. The characteristic test results of the manufactured force sensor, indicated that the nonlinearity error, hysteresis error, and reproducibility errors were each within 0.91%, Therefore it was determined that the manufactured force sensor can be used for checking the spindle tool gripping force.
Keywords:
Force sensor, Gripping force, Spindle, Strain-gage, Rated output1. 서 론
공작물을 가공하는 기계장치 중의 하나인 머신센터는 공구를 고정하여 움직이지 않도록 고정하는 스핀들이 내장되어 있다. 이 스핀들은 유압의 힘으로 고정되는데, 종종 유압장치의 오류가 발생하여 스핀들을 잡아주는 힘이 약할 수 있고, 이로 인해 고속으로 회전하는 스핀들이 이탈하여 사고를 유발하는 경우가 있다. 그러므로 이와 같은 사고를 방지하기 위해서는 스핀들을 잡아주는 파지력을 주기적으로 검사해야한다. 스핀들을 고정하는 유압력(힘)의 측정은 스핀들과 같은 크기로 제작된 파지력 검사기를 사용하고, 이것은 대부분 아날로그 유압계기(지침으로 압력을 표시하는 유압측정기)가 부착한 BT50 스핀들 파지력 검사기를 이용하며, 이 파지력은 2300 kgf정도이다. 머신센터의 파지력을 검사한 값이 2300 kgf 이하인 경우에는 유압장치가 고장이므로 조치를 취해야한다. 스핀들 파지력 검사기를 디지털 검사기로 제작하기 위해서는 스핀들을 당기는 힘을 측정하는 힘센서가 필요하다. 산업체에서 사용되는 기계장치에 부착하여 힘을 측정하는 힘센서[1-7]는 다양한 종류로 연구 개발되었고, 다축 힘센서, 단축 힘센서[8]가 상품화되어 판매되고 있다. 그러나 이 센서들의 형태나 용량이 BT50 스핀들 파지력 검사기의 힘센서로 사용하기에는 적합하지 않으므로 이것을 위한 힘센서를 새롭게 모델링하고 제작하는 것이 필요하다.
본 논문에서는 BT50용 스핀들을 위한 공구 파지력 검사를 위한 힘센서를 개발하였다. 힘센서의 구조를 모델링하였고, 구조해석을 통해 힘센서 감지부를 설계하였으며, 스트레인게이지를 부착하여 힘센서를 제작하였다. 그리고 제작된 힘센서를 특성실험을 실시하였다.
2. BT50용 힘센서 설계 및 제작
2.1 BT50용 힘센서 설계
BT50용 스핀들 공구 파지력 검사기는 기계장치와 제어장치로 구분되나 본 논문에서는 기계장치만 다룬다. Fig. 1은 스핀들 공구 파지력 검사기의 구조를 나타내고 있고, 이것은 고정구(fixture), 힘센서(force sensor), 당김봉 (pulling stick) 등으로 구성된다. 고정구는 검사하고자하는 머신센터의 스핀들을 고정하는 크기와 같게 설계되고, 한쪽 끝에는 힘센서가 고정되고, 중앙 홀에는 당김봉이 조립될 수 있도록 관통되어 있다. 힘센서는 머신센터의 스핀들 고정장치가 당김봉을 당겼을 때, 당기는 힘을 측정하는데 사용되고, 본 논문에서는 이 센서를 설계 및 제작한다. 당김봉은 고정구의 중앙 홀에 조립되고 한쪽 끝은 힘센서의 힘센서의 윗면을 너트로 고정하고, 다른 쪽 끝은 머신센터의 유압장치가 당길수 있는 형태로 설계된다. BT50용 스핀들 검사기는 당김봉을 머신센터의 스핀들 당김장치가 당김봉을 당기면 당김봉이 힘센서의 윗면을 누르므로 힘센서에 힘이 가해지게 되어 머신센터의 유압장치의 당기는 힘을 측정하게 된다.
Fig. 2의 (a)는 BT50용 힘센서의 구조를 나타내고 있다. BT50용 힘센서는 좌측블록, 좌측 감지부, 우측 감지부, 중앙블록, 우측 감지부, 우측블록으로 일체형으로 구성되어 있다. 좌측 블록과 우측 블록은 블록의 아래 평면과 고정판이 고정되고, 이것들의 한쪽 측면은 감지부의 한쪽 끝과 연결된다. 중앙블록은 중앙에는 당김봉이 통과할 수 있는 홀이 있고, 양쪽 측면은 좌측 감지부와 우측 감지부가 연결되어 있다. 좌측과 우측 감지부는 담김봉이 당기는 힘을 감지하기 위한 평판이고, 상부감지부와 하부 감지부로 구분되며, 감지부 위에 스트레인게이지를 부착하여 힘센서를 제작한다. Fig. 2의 (b)는 스트레인게이지 부착위치를 나타내고 있고, S1~S4는 4개의 스트레인게이지를 나타낸 것이다.
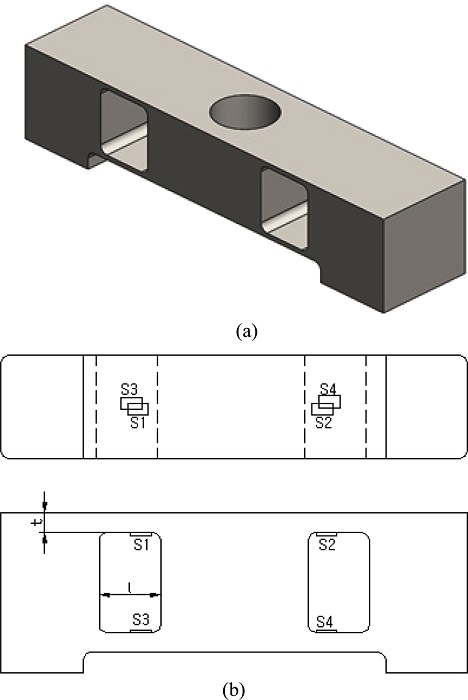
Structure of force sensor for BT50 and location of straingage; (a) Structure of force sensor, (b) Location of straingage.
Fig. 3은 힘센서를 제작할 때 사용되는 휘스톤브리지를 나타내고 있고, T1과 T2는 인장 스트레인게이지, C1과 C2는 압축 스트레인게이지를 나타낸 것이다. Fig. 2의 (b)에서 힘이 센서의 윗방향에서 가해질 때 S1과 S2는 인장 스트레인게이지 부착위치이고, S3와 S4는 압축 스트레인게이지 부착위치이다. 그러므로 힘센서를 제작할 때, 스트레인게이지 부착위치 S1, S2, S3, S4에 각각 스트레인게이지 T1, T2, C1, C2가 부착된다. 힘센서의 정격변형률과 정격출력을 계산하는 식은 각각 식 (1)과 식 (2)와 같이 쓸 수 있다[7].
(1) |
(2) |
여기서 ε은 힘센서의 정격변형률, εT1은 인장 스트레인 게이지 T1 (S1)의 변형률, εC1은 압축 스트레인게이지 C1의 변형률 (S3), εT2은 인장 스트레인게이지 T2 (S2)의 변형률, εC2은 압축 스트레인게이지 C2 (S4)의 변형률, Ei는 토크센서의 입력전압, Eo는 토크센서의 출력전압, K는 스트레인게이지의 상수(약 2.03)이다.
Fig. 4의 (a)는 힘센서를 구조해석하기 위해 작게 나눈 격자(mesh)를 나타내고 있고, 이것은 감지부의 폭방향으로는 3등분하였으며, 길이방향으로는 0.5 mm 간격으로 나누었다. 구조해석 조건은 힘센서의 정격용량이 2,500 kg, 정격변형률 4,000 μm/m, 정격출력 2.0 mV/V, 종탄성계수와 프와송의비가 각각 힘센서의 재질 SUS304인 70 GPa과 0.3이고, 스트레인게이지 부착 위치는 Fig. 2의 (b)에서 나타낸 것과 같이 중앙블록으로부터 4 m와 감지부 폭의 중심선라인인 지점, 8절점 6면체를 선택하였다. 스트레인게이지를 중앙블록으로부터 4 mm 떨어진 위치로 잡은 것은 스트레인게이지를 두 감지부 평판 사이의 안쪽면에 부착위치로 결정하였고 스트레인게이지(N2A-13-S1452-350, 게이지 상수 2.03, 크기 3 mm× 5.2mm)의 크기를 고려하였기 때문이다. 정격하중을 2500 kgf로 결정한 것은 스핀들을 당기는 힘이 2300 kgf이므로 이것보다 크게 하기 위해서이다.
구조해석을 원활하게 진행하기 위해, 힘센서의 전체 크기는 132 mm × 26 mm × 40 mm로 결정하였고, 감지부의 길이와 폭을 각각 15 mm와 26 mm로 결정하였다. 구조해석은 소프트웨어(Solid Works)를 이용하여 좌측과 우측 블록의 아랫부분을 고정시키고, 중앙블록의 위쪽에서 힘센서의 정격용량인 2,500 kg을 가하여 감지부의 두께 t를 결정하기 위해서 실시하였다. Fig. 4의 (b)는 구조해석 결과를 나타내고 있고, 감지부는 예측한 것과 같이 중앙블록쪽으로는 압축, 좌측과 우측 블록쪽으로는 인장으로 변형이 발생되었다. 구조해석으로 결정된 감지부의 크기는 15 mm× 26 mm× 1.0 mm로 결정되었다.
Fig. 5는 힘센서 감지부의 변형률을 나타내고 있고, 가로축은 감지부의 길이, 세로축은 변형률을 나타내고 있으며, 그래프의 좌측 0 mm인 지점이 중앙블록과 결합된 부분이다. 변형률 값이 0 mm/m인 지점은 8.1 mm인 것으로 나타났고, 양쪽 끝지점에서 변형률이 감소한 것은 유한요소의 끝효과 때문이다. 스트레인게이지 부착위치는 중앙블록으로부터 4 mm인 지점이고, 이 지점으로 스트레인게이지 부착위치를 결정한 것은 게이지의 크기(모델: N2A-13-S1452-350, 크기 3 mm× 5.2 mm)를 고려하였을 때, 변형률이 가장 크기 때문이며, 그 지점에서의 스트레인 값은 1030 mm/m이다. 힘센서의 정격변형률은 이 값을 정격변형률을 구하기 위해 식 (1)에 대립하면, 4120 mm/m이었고, 이 값을 기준 정격변형률 4,000 mm/m으로 계산한 정격변형률 오차는 3%이다. 이와 같은 오차가 발생한 것은 감지부의 두께를 0.1 mm 단위로 설계하였기 때문이다. 힘센서의 정격출력값은 식 (2)에 정격변형률값과 스트레인게이지의 게이지상수 2.03을 대입하여 계산하면 2.0909 mV/V이다. 정격출력오차는 기준 정격 출력 2.0 mV/V를 기준으로 계산하면 4.55%이었다.
3. 힘센서의 특성실험결과 및 고찰
BT50용 힘센서는 특성실험을 실시한 후 정격출력, 비직선성 오차, 하중이력, 재현도오차 등의 오차를 계산하여 힘센서로 사용할 수 있는지를 확인해야 한다. 그후 측정장치와 연결하여 교정을 실시해야 BT50용 스핀들 파지력 검사기로 사용될 수 있다. Fig. 7은 BT50용 힘센서의 특성실험장치를 나타내고 있고, 이것은 교정장치(calibration system), 측정장치(measuring system), 추(weight) 등으로 구성되었다. 교정장치는 직사각형 형태의 튼튼한 프레임으로 제작되었고, 측정장치는 DMP40으로 정밀측정에 사용되는 것이고, 추는 힘센서에 하중을 가할 때 사용된다. 힘센서의 특성실험은 추걸이의 상부에 제작한 힘센서를 고정하고 추걸이에 0~2,500 kgf까지 500 kgf 단위로 힘센서의 정격하중인 2,500 kgf까지 증가순으로 추를 이용하여 하중을 가하며, 감소순으로 500 kgf 단위로 하중을 감소시켜 가하여 측정장치로 출력값을 측정하였다.
Table 1은 BT50용 힘센서의 특성실험결과를 나타내고 있고, 이것은 3번 측성실험결과와 평균값이다. 힘센서의 정격출력은 정격하중에서 3번 측정한 값을 평균한 것으로 계산되고, 계산한 결과는 2.0734 mV/V이었다. 비직선성오차는 다음 식으로 계산할 수 있다.
(2) |
여기서, 각 하중에서의 기준값은 정격출력을 각 증가순 하중의 비례식으로 구한 값이다.
하중이력을 계산하는 식은 다음과 같이 쓸 수 있다.
(3) |
재현도오차를 계산하는 식은 다음과 같이 쓸 수 있다.
(4) |
Table 2는 힘센서의 정격출력과 오차들을 나타낸 것이고, 이 오차들은 각각 식 (2)~(4)에 Table 1의 값들을 대입하여 계산한 것이다. 비직선성오차, 하중이력오차, 재현도오차가 0.91%이내 이었으므로 국가에서 지정한 일반계기의 오차 10%를 감안할 때 매우 우수하므로 일반계기로 분류되는 BT50용 스핀들 파지력 검사기의 힘센서로 사용될 수 있다.
4. 결 론
본 논문에서는 BT50용 스핀들 파지력 검사기의 힘센서를 설계 및 제작하였다. 힘센서의 구조는 검사기에 적합하도록 모델링되었고, 구조해석을 통해 힘센서의 감지부 크기가 결정되었으며, 스트레인게이지를 부착하여 힘센서를 제작하였다. 제작한 BT50용 힘센서를 특성실험한 결과, 비직선성오차, 하중이력오차, 재현도오차 등이 0.91%이하로 일반계기로 분류되는 BT50용 스핀들 파지력 검사기의 힘센서로 사용될 수 있을 것으로 판단된다.
추후 연구로는 BT50용 스핀들 파지력 검사기의 측정장치를 설계 및 제작하고, 검사기와 측정장치를 연결한 후 교정검사를 실시하며, 이 검사기를 머신센터에 적용하여 파지력을 검사하는 것이다.
Acknowledgments
논 논문은 2019년도 정부(중소벤처기업부)의 재원으로 중소기업진흥공단의 지원을 받아 수행된 창업성장기술개발 사업 성과임.
REFERENCES
-
S. A. Liu and H. L. Tzo, “A novel six-component force sensor of good measurement isotropy and sensitivities”, Sens. Actuators A Phys., Vol. 100, pp. 223-230, 2002.
[https://doi.org/10.1016/S0924-4247(02)00135-8]
-
H. S. Kim and G. S. Kim, “Design of Two-axis Force/Torque Sensor for Hip Joint Rehabilitation Robot”, J. Inst. Contr. Robot. Syst., Vol. 22 No. 7, pp. 524-529, 2016.
[https://doi.org/10.5302/J.ICROS.2016.16.0067]
-
A. Song, J. Wu, G. Qin, and W. Huang, “A novel self-decoupled four degree-of-freedom wrist force/torque sensor”, Measurement, Vol. 40, pp. 883-891, 2007.
[https://doi.org/10.1016/j.measurement.2006.11.018]
-
J. H. Jung and G. S. Kim, “Design of Force Sensors of Rehabilitation Robot for Knee Rehabilitation”, J. Inst. Contr. Robot. Syst, Vol. 23, No. 1, pp. 46-52, 2017.
[https://doi.org/10.5302/J.ICROS.2017.16.0176]
-
H. S. Kim and G. S. Kim, “Development of Calf Link Force Sensors of Walking Assist Robot for Leg Patients”, J. Sen, Sci. Technol., Vol. 26, No. 2, pp. 114-121, 2017.
[https://doi.org/10.5369/JSST.2017.26.2.114]
-
J. H. Joung and G. S. Kim, "Design of a Force Sensor for Thigh Force Measurement of a Wearable Walking Robot", J. Korean Soc. Precis. Eng., Vol. 34, No. 10, pp. 705-711, 2017.
[https://doi.org/10.7736/KSPE.2017.34.10.707]
- J. H. Park,m and G. S. Kim "Development of Torque Sensor for Measurement of Knee Joint Torque of Walking Assist Robot in Stroke Patients", J. Korean Soc. Precis. Eng., Vol. 27, No. 2, pp. 105-111, 2018.
- ATI Industrial Automation, “Multi-axis forcre/torque sensor”, ATI Industrial Automation, pp. 4-45, 2014.