
Improving the Mechanical Properties of Salt Core through Reinforcing Fibers
This is an Open Access article distributed under the terms of the Creative Commons Attribution Non-Commercial License(https://creativecommons.org/licenses/by-nc/3.0/) which permits unrestricted non-commercial use, distribution, and reproduction in any medium, provided the original work is properly cited.
Abstract
Salt cores have attracted considerable attention for their application to the casting process of electric vehicle parts as a solution to ecological issues. However, the salt core still has low mechanical strength for use in high-pressure die casting. In this study, we investigated the improvements in the bending strength of KCl-based salt cores resulting from the use of reinforcing materials. KCl and Na2CO3 powders were used as matrix materials, and glass fiber and carbon fiber were used as reinforcing materials. The effects of carbon fiber and glass fiber contents on the bending strength properties were investigated. Here, we obtained a new fiber-reinforced salt core composition with improved bending strength for high-pressure die casting by adding a relatively small amount of glass fiber (0.3 wt%). The reinforced salt core indicates the improved properties, including a bending strength of 49.3 Mpa, linear shrinkage of 1.5%, water solubility rate of 16.25 g/min·m2 in distilled water, and hygroscopic rate of 0.058%.
Keywords:
Salt core, Reinforcing fiber, Bending strength, Eco-friendly, High-pressure die casting1. INTRODUCTION
Aluminum high-pressure die-casting (HPDC) alloys have gained significant attention for applications in fields such as theelectronics and automotive industries[1]. They have high strength and stiffness, good formability, a favorable weight ratio, and good corrosion resistance[2,3]. Recently, proposals have been made to perform the casting process using salt cores instead of traditional sand casting; this approach has been widely used to fabricate aluminum die-casting parts. The main reason for this is that the salt-core-based casting process is more suitable for fabricating parts with complex internal geometries and high-quality requirements. Salt-core casting involves using a salt material as a temporary core that can easily be dissolved after the metal solidifies, allowing for the accurate creation of complex internal geometries. Moreover, salt-core casting provides a better surface finish owing to the precise shaping of the salt core. Therefore, for manufacturing undercut structural parts and complicated inner cavities, the salt core has advantages owing to properties such as its high strength, high dimensional accuracy, casting removability, good humidity resistance, and recyclability[4-6]. However, there are still limitations to mass production, such as the strength of the salt core material, vulnerability to humidity, deformation during solidification, and difficulty in extracting the salt core from the mold after casting. The salt core is composed of inorganic salts such as binary or ternary systems, including potassium chloride (KCl), sodium chloride (NaCl), calcium carbonate (CaCO3), sodium carbonate (Na2CO3), and sodium sulfate (Na2SO4). However, these inorganic salts are brittle and do not provide reinforcement. Additionally, salt cores are likely to shrink during cooling and are highly susceptible to cracking, leading to reduced strength[7]. Consequently, it is essential to increase the strength of salt cores. Manufacturing process improvements are currently being made to increase the strength of salt cores. For example, technological developments are ongoing to improve the filling density and uniformity of salt cores during the die-casting process[8,9]. Furthermore, research using simulations is actively being conducted. Many studies have focused on understanding the structure and properties of salt cores and obtaining the optimal conditions for strength improvement through simulations[10,11]. In addition, reinforcing materials such as aluminum borate whiskers, alumina powder, silica powder, silicon carbide whiskers, bauxite powder, quartz powder, mullite powder, and mica powder have been utilized to improve the properties of salt cores[12-14]. These studies have shown that the strength of a salt core without strengthening materials is limited, and when using reinforcements, the liquidity of the molten salt mixtures is limited[15].
Reinforcing fibers are commonly used to reinforce ceramic matrix composites owing to their favorable elastic coefficient, high tensile strength, and exceptional thermal stability. Glass fibers have been investigated as reinforcing fibers to improve salt cores. Gong et al. studied KNO3-based salt cores with various sizes and quantities of reinforcing glass fibers and discussed their microstructures and properties[16]. They reported improved bending strength, and the addition of glass fibers addition reduced the hygroscopic rate and water solubility. Therefore, the addition of glass fibers significantly affected the bending strength of the salt core. As the reinforcing material content increases further, the liquidity of the molten salt decreases, resulting in misrun defects during the casting process. These defects cause large holes in the salt core, significantly affecting its performance.
In this study, inexpensive glass and carbon fibers with low prices were used as reinforcements to strengthen a KCl-based (KCl-60 mol%Na2CO3) salt core. The bending strength of the KCl-based salt core was measured to demonstrate the reinforcing effect of the glass fibers and carbon fibers. Additionally, the water solubility and shrinkage rates were investigated for a performance comparison based on the amount of glass fiber added to the salt core. The morphology and crack microstructures of the KCl-based salt core reinforced using glass fibers were analyzed using scanning electron microscopy (SEM). An optimized composition was obtained to strengthen the salt core with glass fibers. The bending strength of the salt cores improved compared to that of the unreinforced salt core with ultra-low contents (0.3 wt%) of the glass fiber.
2. EXPERIMENTAL
2.1 Raw material
Potassium chloride (KCl, 99% purity) and sodium carbonate (Na2CO3, 99% purity) were used as the matrix materials. Carbon fibers and glass fibers (Keunyung Industrial Corp., Korea) were used as reinforcing materials. The carbon fibers had an average particle size of 100 μm, with a diameter of 7.2 μm, whereas the glass fibers had an average particle size of 20 μm with a diameter of 3 μm. SEM images of the morphologies are shown in Fig. 1.
2.2 Fabrication of KCl-based salt core
The preparation process of the KCl-based salt core is shown in Fig. 2. The initial step involved mixing and drying KCl, Na2CO3, MgCl2, and reinforcing fiber. The molar ratio of KCl, Na2CO3, and MgCl2 was 30 mol%:60 mol%:10 mol%, and the reinforcing fiber contents varied from 0.1 wt.% to 0.7 wt.%. The dried mixture (KCl, Na2CO3, MgCl2, and reinforcing fiber) was then put into an alumina crucible and melted using a furnace at 750 oC. Afterwards, the molten salt was stirred for 10 min. After reaching a temperature of 750 oC, the molten salt was rapidly poured into a preheated metal mold at 220 oC. After cooling for 55 s, the metal mold was opened, and the KCl-based salt core was removed from the mold and cooled to room temperature for solidification. In this way, the KCl-based salt core was completed. The mold used for casting with the salt cores was designed from SKD61 steel, as shown in Fig. 3.
2.3 Measurement and characterization
The mechanical properties of the salt core were primarily evaluated based on its bending strength, which is an important indicator. To determine the KCl-based salt core’s ability to withstand high pressures during pressing, its bending strength was assessed using a three-point bending method on a universal testing machine, DUT-3000CM (Daekyung Engineering Co., Ltd.), at the Korea Testing Laboratory (KTL). The pressure head was kept constant at 2 mm/min with a load of 980 N. Three samples were measured in each group to ensure the accuracy of the test results. The strength of the KCl-based salt core with glass fibers was determined using a strength testing machine. The linear shrinkage rate L was computed using Eq. (1):
(1) |
where l1 represents the designed length of the samples (12 mm) and l2 is the actual length of the samples. The samples used to test the bending strength were cut into cylinders with a height of 45 mm and a diameter of 11 mm. Then, the cylindrical salt cores were used to test the water solubility rate and hygroscopic rate. To determine the water solubility, cylinder samples were immersed in 23±2 oC distilled water in the open atmosphere. The water solubility rate K of the salt cores was calculated using Eq. (2):
(2) |
where m and s represent the mass (g) and total surface area (m2) of the sample, respectively, and t is the dissolution time. The hygroscopic rate ϕ of the KCl-based salt core was calculated according to Eq. (3):
(3) |
where m0 is the original mass of the salt core an individual sample and m1 is the mass exposed to the air (relative humidity 60%) for 1 d using a humidity and temperature controller (Tabai Espec Model PL-2G, -40 to 150 oC, 30-95% RH). The microstructures of the salt core samples previously coated with platinum sputtering were observed and analyzed using a scanning electron microscope (SEM, Inspect 50, FEI, USA).
3. RESULTS AND DISCUSSIONS
Fig. 4 shows the relationship between the bending strength and the additional content of the reinforcing fibers (glass fibers or carbon fibers). As shown in Fig. 4, the carbon fibers and glass fibers have a remarkable effect on the bending strength of the KCl-based salt core. The bending strength of the KCl-based salt core increased as the content of the reinforcing fibers increased. The strength increased from 22 MPa to a maximum of 49.3 MPa at ultra-low glass fiber content (0.3 wt%). The shrinkage rate can help ensure the dimensional precision of the salt cores, as the volume shrinkage is high during the solidification of the salt core.
According to the shrinkage rate results in Table 1, the shrinkage rate tends to increase as the amount of glass fiber increases. The salt core with a 0.3 wt% glass fiber content has a shrinkage rate of 1.5%, and all values are no lower than 4.08%. A lower hygroscopic rate is preferable for storage purposes. Table 1 shows the hygroscopic rate, which compares the moisture resistance characteristics by measuring the weight before and after the humidity exposure period. As the glass fiber content increases from 0 to 0.7 wt%, the moisture resistance gradually increases from 0.036 to 0.122%. This phenomenon occurs because of the high energy boundary between the glass fiber and the salt core, which allows for better moisture absorption between the reinforcing fibers and the salt core, thus increasing the hygroscopic rate.
This allows moisture to be better absorbed between the reinforcing fibers and the salt core, increasing the wet absorption rate. However, at a glass fiber content up to 0.3 wt% in the salt core, the hygroscopic rate remains lower than 0.1%, indicating that the core still possesses moisture resistance. When measuring water solubility, the critical factor is the dissolution time required for the sample to fully dissolve in distilled water. All salt cores with added glass fibers took longer to dissolve than the unreinforced salt cores. Among samples with glass fiber added in the range of 0.1 wt% to 0.5 wt%, similar dissolution times were observed, indicating similar water solubility values. However, samples containing 0.7 wt% glass fiber showed an increase in dissolution time, resulting in the lowest observed water solubility. This phenomenon is attributed to the fact that the glass fiber, as an insoluble material, can impede the water solubility rate of the salt core.
Fig. 5 shows the water solubility experiments of the KCl-based salt core reinforced with 0.3 wt% glass fiber. It appears that the KCl-based salt core enhanced by the glass fiber could dissolve in room-temperature water. As shown in Figs. 5 (a)-(d), when the KCl-based salt core sample was placed in the water at room temperature, the water-insoluble glass fibers gradually separated from the sample. The KCl-based salt core sample completely dissolved after 6 h. The superior water solubility of the salt core is highly advantageous for enhancing the production efficiency of intricate internal cavity components. Additionally, the glass fiber reinforcement can be recycled and reused, thus minimizing the production costs of the salt core.
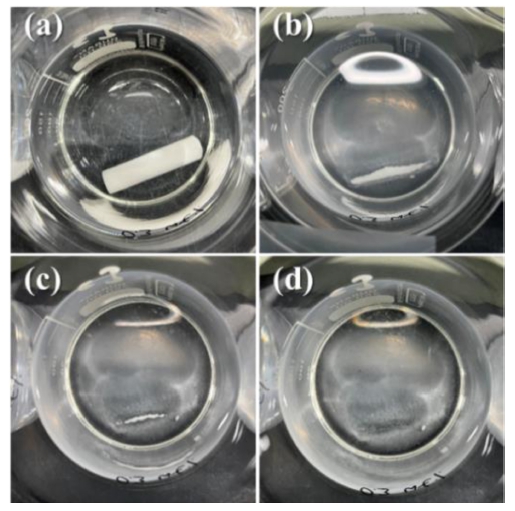
Water soluble experiments of the KCl-based salt core reinforced by 0.3 wt% glass fiber in room temperature: (a) 0 h, (b) 2 h, (c) 4 h, (d) 6 h.
Because the microstructure of materials affects the fracture mechanism, the solidified structures of the salt core samples are shown in Fig. 6. Fig. 6 (a) shows the microstructure of the unreinforced salt core. The solidified structure shows relatively loose integranular adhesion and small micro-holes, indicated by yellow circles. Fig. 6 (b) shows that the microstructure of the salt core sample reinforced with 0.3 wt% glass fiber is compact. Additionally, this micro-morphology shows micro-cracks, as indicated by the arrows. When the introduced reinforcements are well embedded in the salt, crack propagation is impeded because more energy is required for breaking. Moreover, reinforcing fibers with a high melting point can act as foreign crystal nuclei, leading to an increased number and nucleation rate of grains[17]. This hinders the growth of columnar crystal grains, resulting in a higher strength of the salt core reinforced with these fibers[9].
4. CONCLUSIONS
In this study, the effects of reinforcing fiber content on bending strength were investigated. We successfully fabricated a complex high-strength salt core with a favorable morphology. We used glass fibers and carbon fibers as reinforcing fibers, which can inhibit crack propagation in the KCl-based salt core. The addition of a very small content (only 0.3 wt%) of glass fiber to the salt core improves the bending strength. The microstructure of the fractured surface was investigated to demonstrate this effect. Moreover, the water solubility rate, hygroscopic rate, and shrinkage properties of the KCl-based salt core reinforced with glass fibers were obtained. It was found that the enhanced bending strength of the salt core ranged from 22 to 49 Mpa.
Acknowledgments
This research was supported by the Promising Green New Deal Company 100 R&D Program (2MRC190) funded by the Ministry of SMEs and Startups(MSS, Korea)
REFERENCES
-
J. Bedmar, B. Torres, and J. Rams, “Manufacturing of Aluminum Matrix Composites Reinforced with Carbon Fiber Fabrics by High Pressure Die Casting, Mater., Vol. 15, No. 9, pp. 3400(1)-3400(18), 2022.
[https://doi.org/10.3390/ma15093400]
-
S. O. Akinwamide, O. J. Akinribide, and P. A. Olubambi, “Microstructural evolution, mechanical and nanoindentation studies of stir cast binary and ternary aluminium based composites, J. Alloys Compd., Vol. 850, pp. 156586(1)-156586(3), 2021.
[https://doi.org/10.1016/j.jallcom.2020.156586]
-
S. O. Akinwamide, B. T. Abe, O. J. Akinribide, B. A. Obadele, and P. A. Olubambi, “Characterization of microstructure, mechanical properties and corrosion response of aluminium-based composites fabricated via casting—a review,J. Adv. Manuf. Technol., Vol. 109, pp. 975-991, 2020.
[https://doi.org/10.1007/s00170-020-05703-1]
-
J. Weise, J. Hilbers, F. Handels, D. Lehmhus, M. Busse, and M. Heuser, “New Core Technology for Light Metal Casting, Adv. Eng. Mater., Vol. 21, No. 4, p. 1800608, 2019.
[https://doi.org/10.1002/adem.201800608]
-
M. Gromada, A. Świeca, M. Kostecki, A. Olszyna, and R. Cygan, “Ceramic cores for turbine blades via injection moulding, J. Mater. Process Technol., Vol. 220, pp. 107-112, 2015.
[https://doi.org/10.1016/j.jmatprotec.2015.01.010]
-
H. Khandelwal and B. Ravi, “Effect of Binder Composition on the Shrinkage of Chemically Bonded Sand Cores, Mater. Manuf. Process., Vol. 30, No. 12, pp. 1465-1470, 2015.
[https://doi.org/10.1080/10426914.2014.994779]
-
P. Jelinek, E. Adamkov, F. Miksovsky, and J. Beno, “Advances in Technology of Soluble cores for Die Castings, Arch. Foundry Eng., Vol. 15, pp. 29-34, 2015.
[https://doi.org/10.1515/afe-2015-0032]
-
P. P. Zhou, G. Q. Wu, Y. Tao, X. Cheng, J. Q. Zhao, and H. Nan, “Optimization of the injection molding process for development of high performance calcium oxide -based ceramic cores, Mater. Res. Express, Vol. 5, No. 2, p. 025208, 2018.
[https://doi.org/10.1088/2053-1591/aaaeec]
-
R. Huang and B. Zhang, “Study on the Composition and Properties of Salt Cores for Zinc Alloy Die Casting, Int. J. Metalcasting, Vol. 11, pp. 440-447, 2017.
[https://doi.org/10.1007/s40962-016-0086-7]
- M. Lagler, “Use of Simulation to predict the Viabilirt of Salt Cores in the HPDC Process-Shot Curve as a Decisive Criterion, Die Casitng Eng., Vol. 57, No. 4, pp. 16-17, 2013.
-
B. Fuchs, H. Eibisch, and C. Körner, “Core Viability Simulation for Salt Core Technology in High-Pressure Die Casting, Int. J. Metalcasting, Vol. 7, pp. 39-45, 2013.
[https://doi.org/10.1007/BF03355557]
- J. Yaokawa, K. Anzai, Y. Yamada, H. Yoshii, and H. Fukui, “Castability and Strength of Potassium Chloride-Ceramic Composite Salt Cores, J. Japan Foundry Eng., Vol. 76, No. 10, pp. 823-829, 2004.
-
J. Beòo, E. Adámkov, F. Mikovsk, and P. Jelínek, “Development of composite salt cores for foundry applications, Mater. Technol., Vol. 49, No. 4, pp. 619-623, 2015.
[https://doi.org/10.17222/mit.2013.160]
-
J. Yaokawa, D. Miura, K. Anzai, Y. Yamada, and H. Yoshii, “Strength of Salt Core Composed of Alkali Carbonate and Alkali Chloride Mixtures Made by Casting Technique, Mater. Trans., Vol. 48, No. 5, pp. 1034-1041, 2007.
[https://doi.org/10.2320/matertrans.48.1034]
-
F. Liu, S. Tu, X. Gong, G. Li, W. Jiang, X. Liu, and Z. Fan, “Comparative study on performance and microstructure of composite water-soluble salt core material for manufacturing hollow zinc alloy castings, Mater. Chem. Phys., Vol. 252, p.123257, 2020.
[https://doi.org/10.1016/j.matchemphys.2020.123257]
-
X. Gong, W. Jiang, F. Liu, Z. Yang, F. Guan, and Z. Fan, “Effects of glass fiber size and content on microstructures and properties of KNO3-based water-soluble salt core for high pressure die casting, Int. J. Metalcasting, Vol. 15, pp. 520-529, 2021.
[https://doi.org/10.1007/s40962-020-00480-9]
-
S. Tu, F. Liu, G. Li, W. Jiang, X. Liu, and Z. Fan, “Fabrication and characterization of high-strength water-soluble composite salt core for zinc alloy die castings, Int. J. Adv. Manuf. Tech, Vol. 95, pp. 505-512, 2018.
[https://doi.org/10.1007/s00170-017-1208-y]