
Emulsion Electrospinning of Hydrophobic PTFE-PEO Composite Nanofibrous Membranes for Simple Oil/Water Separation
This is an Open Access article distributed under the terms of the Creative Commons Attribution Non-Commercial License(https://creativecommons.org/licenses/by-nc/3.0/) which permits unrestricted non-commercial use, distribution, and reproduction in any medium, provided the original work is properly cited.
Abstract
Polytetrafluoroethylene (PTFE) fibers are widely used in the textile industry, filter media, membrane distillation, electronic appliances, and construction. In this study, PTFE–polyethylene oxide (PEO) fibrous membranes were fabricated by emulsion electrospinning; subsequently, pure PTFE nanofibers were obtained via sintering. PTFE–PEO electrospinning solutions were prepared using different weight ratios to determine the optimized condition. As the ratio of the PEO increased, the fiber structure improved. Scanning electron microscopy and Fourier-transform infrared spectroscopy observations indicate that PEO is removed and PTFE fused gradually to form bonds among them during sintering. The obtained pristine PTFE membrane demonstrated hydrophobicity at 143.6° water contact angle and oleophilicity at 0° oil contact angle, which is known to be utilized for oil/water separation. A simple separation experiment was performed to remove oil droplets from water. The PTFE membrane exhibited good chemical stability and a high surface-area-to-volume nanofiber ratio. These excellent properties suggest that it is applicable to oil/water separation in harsh chemical environments.
Keywords:
electrospinning, PTFE, oil/water separation1. INTRODUCTION
Polytetrafluoroethylene (PTFE) is well known for its outstanding thermal stability, chemical resistance, low surface energy, and good electrical insulation [1-5]. PTFE fibers are widely used in the textile industry, filter media, membrane distillation, electronic appliances, and construction [6,7]. PTFE membrane are generally prepared by stretching and porousizing sheets formed by molding PTFE powder. These conventional PTFE membrane manufacturing techniques pose a disadvantage, in that continuous processes are difficult to perform and the average pore size cannot be controlled easily.
In recent years, electrospinning technology has received significant attention, due to its low energy consumption and as an environmentally friendly method for preparing nanofibers [8,9]. Fibrous mats fabricated through electrospinning are highly porous with large surface areas. During electrospinning, electrostatic force is generated between a needle and a collector to produce fine fibers from a charged polymer solution or melt. As charges begin to accumulate within the polymer solution, the repulsive forces among charges can overcome the weaker forces of surface tension of the polymer solution, which then erupts into a polymer solution jet that travels to the grounded collector, during which the solvent included in the polymer solution dries out and only the polymer fiber remains. The diameters of the fabricated fibers range from a few nanometers (nm) to several micrometers (μm).
Electrospinning technology, however, is not readily applicable to PTFE nanofiber formation, as PTFE is much more challenging compared with other polymers that can be easily dissolved in various organic solutions. Owing to the high chemical resistance and thermal stability of PTFE, it is almost impossible to directly obtain/maintain a PTFE solution for electrospinning. Hence, a feasible eco-friendly method for fabricating electrospun fibrous membranes has been proposed, known as emulsion electrospinning. The method utilizes the mixture of a water-based emulsion of the desired polymer that is to be electrospun and a water-soluble carrier polymer for fabricating composite fibers [10-13]. A fiber fabricated through such electrospinning method comprises primarily of the carrier polymer filled with the desired polymer in the form of emulsion beads. To acquire a pure electrospun fiber comprising the desired polymer, a sintering step is performed to process the polymer beads into continuous fibers by eliminating the organic carrier.
In the present study, we further investigate the PTFE nanofibrous membrane forming mechanism as well as its wettability behavior, and oil/water separation performance. Specifically, a hybrid polyethylene oxide PTFE-PEO nanofibrous membrane was first prepared by electrospinning; subsequently, after a sintering treatment, PEO nanofibers were decomposed and a pure PTFE nanofibrous membrane remained. A detailed investigation into the morphology and chemical component variations during sintering was first conducted to reveal the forming mechanism of the membrane. Subsequently, the wettability of the membrane was evaluated. A demonstrative usage of the fabricated PTFE membrane for oil/water separation was performed to show its applicability to oil/water separation.
2. EXPERIMENTAL
2.1 Membrane material
An aqueous PTFE dispersion (60 wt%) was purchased from Chemours Co. Ltd. (China). PEO with a molecular weight of 600,000 gmol-1 was purchased from Sigma–Aldrich.
2.2 Membrane preparation
First, a PEO aqueous solution was prepared by dissolving 4 g of PEO powder in 96 g of water at 40 °C under constant stirring for at least 6 h. The PTFE emulsion was added to the PEO solution with constant stirring for at least 1 h. PTFE–PEO solutions were prepared at various weight ratios of PEO:PTFE (1:99, 2:98, 2.5:97.5, and 3:97)
The electrospinning system of composite PTFE–PEO membrane comprises a high-voltage source, a syringe pump, and a stainless-steel mesh as the collector. The electrospinning process was performed at an applied voltage of 15 kV, a spinning distance of 15 cm, and a fluid flow rate of 0.5 ml/h. After more than 3 h of electrospinning, the membrane was separated from the mesh. The electrospun membrane was sintered in a furnace at 380 °C for 10 min. Subsequently, the furnace was reduced gradually to 30 °C in 8 h. During the sintering process, a N2 atmosphere was maintained.
2.3 Membrane Characterization
The morphology was evaluated by scanning electron microscopy (SEM; Mini SEM) after it was vacuum coated with a thin layer of gold. Fourier transform infrared spectroscopy (FT-IR; Model Nicolet iS50, Thermo Fisher Scientific) was performed to determine the fiber chemical composition. The water contact angle (WCA) and oil contact angle (OCA) were determined using a droplet analyzer (SDL200TEZD, FEMTOFAB Co., Ltd, Korea).
3. RESULTS AND DISCUSSIONS
3.1 Membrane Morphology
The fiber morphology was analyzed through SEM. Fig. 2 presents the SEM images of the fiber morphologies at different weight ratios (1:99, 2:98, 2.5:97.5, and 3:97) of PEO: PTFE. When the PEO ratio was the lowest, discontinuous fibers and beads were obtained. At higher PEO ratios, more uniform fibers were observed. This occurred because small quantities of PEO could not bind the PTFE nanoparticles together. When the PTFE-PEO mass ratio was 97:3, uniform fibers were obtained. Therefore, a membrane with a PTFE–PEO mass ratio of 97:3 was used for the subsequent sintering process.
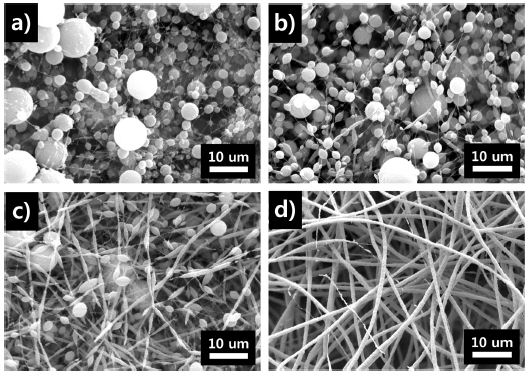
SEM image of PTFE–PEO membranes with different weight ratios of PEO:PTFE (a)1:99 (b) 2:98 (c)2.5:97.5 (d)3:97
Fig. 3 shows an SEM image of electrospun PTFE-PEO nanofibers after sintering. During sintering, PEO decomposed, whereas PTFE fused gradually and formed bonds between them. Owing to the aggregation of PTFE particles, the fiber surface was rough. The average diameter of the PTFE–PEO nanofibers were 950 μm before sintering, but the diameter decreased to 750 nm as the PEO was removed during sintering.
3.2 Chemical Component of the Membrane
To confirm the composition of the nanofibers before and after sintering, we performed FT-IR on the samples. FT-IR (Model Nicolet iS50, Thermo Fisher Scientific) was used to analyze the chemical composition of the fabricated membrane component. Figure 4 shows the FT-IR spectra for (a) PEO powder, (b) PTFE particles, and PTFE membrane (c) before and (d) after sintering. The peaks at 2888 cm-1, 1466 cm-1 were due to the stretching of C–H and C–H2. Furthermore, 1145 cm-1 is associated with C=O bonding. These are PEO components. Comparing the samples, it is apparent that all the absorption peaks associated with PEO bonding disappeared, whereas the absorption of C–F bonding peaks at 1201 cm-1,1145 cm-1 remained. Furthermore, PEO was removed and PTFE membranes were obtained.
3.3 Wetting Characteristics of the Membrane
PTFE exhibit good waterproof properties. To confirm the PTFE membrane’s superhydrophobic characteristics, we performed contact angle measurements, after a water/oil separation. Fig. 6 shows the WCA and OCA of the PTFE membrane. The average measured WCA of the PTFE membrane was 143.6°, indicating its hydrophobic nature. However, the PTFE membrane is completely wetted by oil (OCA: 0°). PTFE exhibits both hydrophobic and oleophilic properties and has been utilized for oil/water separation. A simple experiment was performed to remove oil droplets on water [Fig. 7]. The results demonstrated that the oil droplets were effectively removed, suggesting its potential for water/oil separation applications. The PTFE membrane demonstrated good chemical stability and a high surface-area-to-volume ratio of nanofibers. Therefore, it is applicable to oil/water separation in various chemical environments.
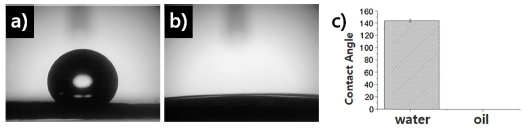
(a) Water droplet on the membrane; (b) oil droplet on the membrane; (c) water/oil contact angle of PTFE membrane.
4. CONCLUSIONS
The fabrication of PTFE membranes by electrospinning is difficult because PTFE can barely dissolve in any solvent. We fabricated a PTFE membrane through emulsion electrospinning. PTFE–PEO electrospinning solutions were prepared with different weight ratios. As the ratio of the PEO increased, the fiber structure improved. At the PTFE–PEO weight ratio of 97:3, we obtained uniform nanofibers. Furthermore, we obtained pure PTFE nanofibers after sintering at 380 °C. We confirmed through FT-IR spectra that PEO disappeared in PTFE–PEO nanofibers, whereas pristine PTFE remained throughout the sintering process. The membrane showed a WCA of 143° and an OCA of 0°, suggesting its applicability for oil/water separation. A simple oil/water separation experiment was conducted to determine whether the hydrophobic/oleophilic membrane is applicable to water/oil separation. The fabricated membrane readily removed oil droplets floating on the water surface. The PTFE membrane offers advantages of superb chemical stability and high surface-area-to-volume ratio of nanofibers. These excellent properties suggest that it can be used for oil/water separation in harsh chemical environments.
Acknowledgments
This work is supported by SYNOPEX INC.
References
-
E. N. Brown and D. M. Dattelbaum, “The role of crystalline phase on fracture and microstructure evolution of polytetrafluoroethylene (PTFE)”, Polymer, Vol. 46, No. 9, pp. 3056-3068, 2005.
[https://doi.org/10.1016/j.polymer.2005.01.061]
-
H. Z. Feng Wang, H. Zhang, H. Tang, J. Chen, and Y. Guo, “An elastic microporous material with tunable optical property”, Mater. Lett, Vol. 164, pp. 376-379, 2016.
[https://doi.org/10.1016/j.matlet.2015.10.158]
-
Q. L. Huang, C. F. Xiao, X. Y. Hu, and X. F. Li, “Study on the effects and properties of hydrophobic poly(tetrafluoroethylene) membrane”, Desalination, Vol. 277, No. 1-3, pp.187-192, 2011.
[https://doi.org/10.1016/j.desal.2011.04.027]
-
T. Kurose, T. Takahashi, and K. Koyama, “A New Proc`ess to Make a Porous PTFE Structure from Aqueous PTFE Dispersion with the Help of Hydrogel”, J. Porous Mater.,Vol. 11, pp. 173-181, 2004.
[https://doi.org/10.1023/B:JOPO.0000038013.74364.50]
-
S. K. Biswas and K. Vijayan, “Friction and wear of PTFE - a review”, Wear, Vol 158, No. 1-2, pp. 193-211, 1992.
[https://doi.org/10.1016/0043-1648(92)90039-B]
-
K Xiao, J Sun, Y Mo, Z Fang, P Liang, and X Huang, “Effect of membrane pore morphology on microfiltration organic fouling: PTFE/PVDF blend membranes compared with PVDF membranes”, Desalination, Vol. 343, pp. 217-225, 2014.
[https://doi.org/10.1016/j.desal.2013.09.026]
-
S. J. Zhu, Y. Y. Zhou, O. Takashi, and G. Wu, “Preparation of Polytetrafluoroethylene Ultrafine Fiber Mats with Electrospinning Process”, Materials, Vol. 675-677, pp. 827-830, 2011.
[https://doi.org/10.4028/www.scientific.net/MSF.675-677.827]
-
G. Moradi, S. Zinadini, L. Rajabi, and S. Dadari, “Fabrication of high flux and antifouling mixed matrix fumarate-alumoxane/PAN membranes via electrospinning for application in membrane bioreactors”, Appl. Surf. Sci.,Vol. 427, pp. 830-842, 2018.
[https://doi.org/10.1016/j.apsusc.2017.09.039]
-
S. Yang, P. Lei, Y. Shan, and D. Zhang, “Preparation and characterization of antibacterial electrospun chitosan/poly (vinyl alcohol)/graphene oxide composite nanofibrous membrane”, Appl. Surf. Sci., Vol. 435, pp. 832-840, 2018.
[https://doi.org/10.1016/j.apsusc.2017.11.191]
-
W. Qing, X. shi, Y. Deng, and W. Zhang, “Robust superhydrophobic-superoleophilic polytetrafluoroethylene nanofibrous membrane for oil/water separation”, J. Membr., Vol. 540, pp. 354-361, 2017.
[https://doi.org/10.1016/j.memsci.2017.06.060]
-
J. Xiong, P. Huo, and F. K. Ko, “Fabrication of ultrafine fibrous polytetrafluoroethylene porous membranes by electrospinning”, J. Mater. Res.,Vol. 24, pp. 2755-2761, 2009.
[https://doi.org/10.1557/jmr.2009.0347]
-
C. Su, Y. Li, H. Cao, C. Lu, Y. Li, and J. Chang, “Novel PTFE hollow fiber membrane fabricated by emulsion electrospinning and sintering for membrane distillation”, J. Membr.,Vol. 583, pp. 200-208, 2019.
[https://doi.org/10.1016/j.memsci.2019.04.037]
-
Y. Feng, T. Xiong, S. Jiang, S. Liu, and H. Hou, “Mechanical properties and chemical resistance of electrospun polyterafluoroethylene fibres”, RSC adv., Vol. 26, pp. 24250-24256, 2016.
[https://doi.org/10.1039/C5RA27676D]